The steel of the file has already been forged and hardened.
Follow along as I tell you how to make a knife.
Make two of them and attach them to the knife with three rivets peened over tight with a hammer. When you cut out a profile for your knife, youll have the luxury of clarity and can move on to the next stage.
Advice youll never hear from the mainstream media.
If you try and make a knife out of cold rolled steel, the type you can buy at a hardware store or steel supply, youre going to be very disappointed.
I'm playing it fast and loose, so I used a flap disc and an angle grinder. I found that there is a wide range of steels used.
It is, therefore, a necessity to pay as much attention to the finish of your knife as you have put into the making of the blade itself.
Thanks for making it look as if I may have the chance to do the same.
It doesnt matter if your design is bright or not, as long as it provides a clear picture.
How To Ensure Your Livestock Survive The Winter, 8 Foolproof Ways To Heat Your Home When The Powers Out, 10 Cyber Safety Tips to Protect Your Browsing, Why Almost Everyone Is Wrong About Cooking With Lard, Surviving Extreme Heat Without Air Conditioning, The Best (And Safest) Way To Stockpile Gasoline, 4 Less-Than-Lethal But Effective Weapons For Home Defense.
That looks like some very nice craftsmanship. I inverted the sander and put it in the bench vise.
If we are careful not to lose the temper in the steel, we can avoid the problem of having to re-temper it.
At this point, a file should skate right off the steel.
Instead of condemning your equipment to the junkyard, you can quickly deploy it to use in other vital endeavours such as carving a knife out of its blades. About: Freelance writer and full-time maker.
In other words, it is vital to have a pattern for the knife you have in mind, whether its something someone else has done before or an entirely original idea.
The bandsaw steel is slightly on the thinner side of ideal in my opinion but still thick enough for the blades Ive been making.
Cut the scales to the rough size you need, then cut them in half.
Blades from a diamond saw are from soft steel as opposed to the general hard steel.
This means it's safe to add wood, so that's next.
Tempering should lessen the chance of it breaking. When you have successfully cut out your knife pattern and filed the steel to taste, it becomes vital to work on your knife handle.
Angle Grinder (with cutoff wheels and flap disc), Saw suitable for cutting small pieces of wood, 10" table saw blade or other source of steel, Bricks (preferably fire bricks, but regular red bricks work too). Like earlier said, lots of knives models take after other peoples designs, and theres no crime if your knife also follows this pattern. Great write up Bill! Finally got through with a masonry bit.
Good shit. Play with it and see what works.
Flaxseed oil works.
Put an edge on the knife.
Now we're going to get the steel super hot to harden it. These finishes abound as a result of the fact that there are millions of knife models in the world today.
5 years ago. Before attaching the blade to the support block, make a line down the center of its thickness.
For rough shaping, I used the same angle grinder with the same flap disc. Drop you temperature down to 1475 - 1500 F, quench again, temper at 400 F and try the snap test again. You will end up with a blade that is wavy and inconsistent.
I used 1/8" brass rod and cut it with a dull hacksaw (dullness is optional). Thanks for the well written steps.
You see if the steel is removed with a cutting torch it will be compromised. Damn near wore out ever drill bit I had tryna get three 1/4 inch rivet holes in the damn thang.
This post was contributed by a community member.
There are numerous ways to finish your knife when youre making it from a diamond saw blade.
In other words, it is vital to have a pattern for the knife you have in mind, whether it, s something someone else has done before or an entirely original idea.
Stop just short of sharpening the knife blade, as you will put the edge on the knife with a honing stone.
You can use a diamond saw blade in numerous capacities, some of which include; cutting through concrete, stones, bricks, asphalt and many more.
You can also make very thin knives out of reciprocating saw (sawzall) blades as well.
I was wondering if that would work when I saw the size of the circular saw. Otherwise your knife is gonna look goofy. It will lose both its hardness and temper, making it useless as a knife steel.
If you only have one tool with you at all times, it has to be a knife. what type of steel is this knife gonna contain?
So I got my Harbor Freight angle grinder and my HF files and some sandpaper and the blade that came with my (used) table saw and I got to work. The views expressed in this post are the author's own.
This is necessary, especially when grinding the second side, to prevent the knife from coming off.
This will provide you with a gauge line for knowing when you are approaching the halfway point in grinding. That's good, but we can't leave it like this.
While you may be able to sharpen it, the edge will dull extremely easily.
Its not clear in the photo, but I used double-sided masking tape for this.
It'll get there. As you continue to make knives, it will go faster and get easier.
Horse shoeing rasps are available at farm supply stores, as well as a number of online suppliers. Then draw a knife profile with a felt marker. congrats to your first Instructable and being featured!
It doesn.
By using our services, you agree to our use of cookies. Most of us buy our knives at a store. Use a file for fine detail unless you're very, very good with the grinder. I just wish I didn't put my old table saw blade in the weekly recycle bin a few months ago :(. I then attached the handles with superglue (epoxy is also good), inserted the pins, and peened them over with a hammer. This handle makes your knife more natural to use and, of course, more beautiful. It is incredibly easy to fashion out a shiv from your old, and unused diamond saw blade.
They get some significant scale, but it cleans up nicely and is very grindable after that.
All three can, of course, be crafted from the comfort of your home and still retain as much efficacy as those made by the professionals. The second step to making a knife from your old diamond saw blade is to cut out the shape of your desired knife from the template.
Are these sawblades generally good stock for knives?
The video and music is great too.
The facing side has been ground all the way, but the reverse side has not been. This caused the ground portion of this blade to be 7/16 wide.
I think Mick hit the mark with the "have a lot of fun with them" statement.
You can grind a knife blade with either a belt sander or a bench grinder.
A hand saw will work just fine.
The first knife is I made 30 years ago was out of a giant circular saw blade that was probably 100 years old. I have made several machetes out of those type of bandsaw blades.
Really allowed me to read this in your voice lol.
Section 2: How to Use Your Old Diamond Saw Blade, Section 3: Making blades the materials you need to prepare, Section 4: Five Steps Teach you Step By to Step to Make a Knife.
A diamond saw blade is a compelling piece of equipment, but just like any other power equipment, it cannot be in active use forever.
You want to take material off the blade along the entire edge in one stroke; working your way from the handle end to the point. Unless you are good at trigonometry, the easiest way to figure out the angle for your blade is to draw various angles on a sheet of paper and measure how far back the blades taper goes for the thickness of your knife blank. That means that the blade is shaped and the edge thinned by hammering it while it is heated, rather than just cutting it out.
Soon you'll even be able to keep up with all the requests for your knives. I know the "right" way to do it, and that's my next project, but I wanted to see how I'd do using only cheap tools and cheap materials.
To grind the taper on the blade, you will need something to hold the knife blade at the correct angle.
Of all the survival equipment available, the most useful and most necessary is a good knife. Using soft steel to craft your knife will cut down the whole manufacturing process by two or more steps as you no longer have to file your iron until its ready for use in the home. Like other files, these are made of a high grade, hardened steel, which will hold an edge well.
Lots of oils work. It's really tough stuff.
Concrete saw blades that are diamond tipped are made of either 4140, or 4130, depending on the diameter.
Sign up for Off The Grid News weekly email and stay informed about the issues important to you, featured how to make a knife how to make knives knife knife blade knives stainless steel. If heat treating and tempering are no big deal to you, then you can cut this steel any way you want. If you want a better quality knife, you should grind the bevel using a file and a jig to obtain the correct angle. He showed me how to make blades from my old blades, a valuable lesson, which Im about to teach you in this article.
Best of luck to you. You have inspired me to no end. Awesome cant wait to see more knives from you in the future. Location: Cebu, Philippines (or Michigan, USA), I looked into lapidary blades last year because I had a source.
My Brother-in-law made some sweet twin Tanto Knives!
It can last as long as any other service equipment but is also prone to wear and tear and will no longer be of any use in cutting through the hardest substances. He has the very best selection of tool steel for knife makers that I have been able to find. I cut some test strips, heated them up to about 1600 degrees and quenched them. It's now time to cut out the knife blank. For work, this knife A little toothpick I made.
Saws with broken handles and light rusting can buy cheaply.
Unless you have the capability of forging, you are limited by the steel you can get.
Wish me luck!
Snaping at 30 degrees proves hardness.
They just don't work quite as well.
To do this, we use a torch and some bricks to contain the heat.
The wooden pieces used as a handle on this knife are called slabs.
I love the way you spelled figgered. If you need to work on one area to catch up with the rest of the blade, make a few passes through that area and then go back to full length passes. It's easy and will be very handy for you in the future when you make knives. If you prefer video, you can check that out here: https://youtu.be/V91Btmi7oNU.
Be careful as you dont want to heat up the knife blade while grinding it. European one are sometimes 15N20.
Wife got me this for my birthday, had a crack that goes two more balisongs i made, one live blade & one trainer, Another small boot dagger I did in cpm154 and linen micarta, Press J to jump to the feed. Easily 15/20 knives each bandsaw blade, then with three of those AND the saw?
Repeat the grinding process on this side of the knife, to make it match the first side.
Very nice.
Be especially careful about not overheating the tip; as it thins, it will overheat much easier. Im not home to go measure it at the moment but I love it. You're not going to hurt anything. Therefore, they dont hold an edge as well as high carbon steel knives do. Badass!
Usually they gwt discarded if they can't be repaired or the mill gets shut down. Try to keep them in line with one another and roughly parallel to the spine (back edge) of the blade or it'll look weird. Grinding a knife blade takes a light touch. You cant make a good quality knife, without having good quality steel to start with.
By the end, the wood felt like glass. But if you want the steel to remain strong start cutting this steel with cold chisels and hammers to get knife blanks and take a shortcut around the heat-treating process altogether. This removed the scratches from all of the previous work and left a really nice finish.
I have been using the larger (24" and bigger)blades for a couple of years now and find if I normalise them the HT like 01 they come up hard and tough.
Regular bricks will do in a pinch. t matter if your design is bright or not, as long as it provides a clear picture. I got it at a scrap yard for 5 dollars and cut it out with a 4 inch grinder.
Some are low carb. The Essential Survival Secrets of The Most VigilantMost SkilledMost Savvy Survivalists in the World!
Here comes the time-consuming part: shaping.
Bring it home, remove the handle and clean it up with fine sandpaper and mineral spirits. You consent to our cookies if you continue to use our website. Files are made of steel that will hold an edge well, as it is necessary for the file to not become damaged when used to shape metal.
Making a knife out of your old diamond saw blade can be one of the best decisions for your diamond saw machine, but it is nevertheless a simple yet tasking procedure that takes a lot of time and dedication especially if you, There are numerous ways to finish your knife when you.
I added a thumb relief with a half-round file because I liked how it felt.
The diamond blade has diamonds fitted on its edge for cutting through solid or harsh substances.
Most people know it as a component of Damascus but its also a very respectable blade steel on its own.
It's simple and food-safe and doesn't stink.
A couple of years ago, I hosted a couple of friends to dinner at my private residence.
There are three essential types of the diamond saw blade, which are the circular saw blade; the diamond gang saw blade and the diamond band saw blade.
Start by scribing a line across the saw blade and clamping it down securely. After the Heat treat Hardening Quench, the blade will be hard, but also brittle. You can buy pretty much any style of knife you want, in just about any size and manufactured to just about any quality level. Most modern knives are made of stainless steel. I used beeswax and orange oil to finish the scales. Written by: Rich M How-To 9 Comments.WP-PrintIcon{margin-bottom:-3px}Print This Article. Even so, it can be nice to make your own. So instead of it receding it would bump out at the top.
Have a look at The New Jersey Steel Baron.
You can make kitchen and filet knives from carpenters' saws or much bigger and stronger knives from thicker crosscut saws that were used to fell trees. Old files are often made of high carbon steel. Theres no sense going to all the trouble of making yourself a knife, only to have it break.
You just made a knife!
They enjoy widespread usage as a result of the fact that each diamond saw type design hinges towards a different custom uses. Copyright 2009-2022 NCcuttingtools.com |.
The one I used was a good blade when it was new and it hardened quite well, but trial and error is the only way you're going to be able to find out. Some newer types of stainless steel have a higher carbon percentage, more closely matching the molecular structure of high carbon steel knives.
This has the potential to overheat the steel and cause problems later on, so I would not recommend doing this with expensive tool steel or any knife you plan to sell. The last phase requires a light touch.
I used spray glue to attach 800/1000/2000 grit paper to a scrap of wood and used it to polish the sides of the knife. Thats a hard balance to reach.
Problem is that they are a blue eyed bitch to cut and drill unless you do a complete spheriodal anneale. Let the grinder do the work and don't force it.
Grinders aren't great at making curved cuts so this helps a lot.
Be careful, because the inside will get ridiculously hot.
Drill three holes in the handle area for rivets.
Sharpening is too complex to cover here, but the basic idea is to start with a coarse stone and move up to a fine one until you have a nice edge on your knife. Off The Grid News is an independent, weekly email newsletter and website that is crammed full of practical information on living and surviving off the grid. If you know, that would be awesome.
We are going to grind the knife blade to shape, rather than forging it.
I drew an outline of the blade on the metal using a sharpie, then made relief cuts with the grinder. Ideally, a knife blade needs to be hard enough to sharpen well and maintain an edge, while not being so hard that it chips easily.
Follow along as I tell you how to make a knife.
Make two of them and attach them to the knife with three rivets peened over tight with a hammer. When you cut out a profile for your knife, youll have the luxury of clarity and can move on to the next stage.
Advice youll never hear from the mainstream media.
If you try and make a knife out of cold rolled steel, the type you can buy at a hardware store or steel supply, youre going to be very disappointed.
I'm playing it fast and loose, so I used a flap disc and an angle grinder. I found that there is a wide range of steels used.
It is, therefore, a necessity to pay as much attention to the finish of your knife as you have put into the making of the blade itself.
Thanks for making it look as if I may have the chance to do the same.
It doesnt matter if your design is bright or not, as long as it provides a clear picture.
How To Ensure Your Livestock Survive The Winter, 8 Foolproof Ways To Heat Your Home When The Powers Out, 10 Cyber Safety Tips to Protect Your Browsing, Why Almost Everyone Is Wrong About Cooking With Lard, Surviving Extreme Heat Without Air Conditioning, The Best (And Safest) Way To Stockpile Gasoline, 4 Less-Than-Lethal But Effective Weapons For Home Defense.
That looks like some very nice craftsmanship. I inverted the sander and put it in the bench vise.
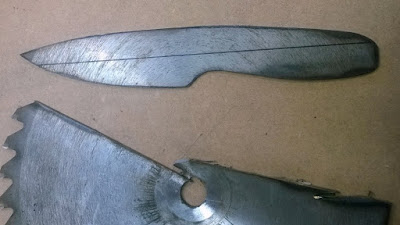
If we are careful not to lose the temper in the steel, we can avoid the problem of having to re-temper it.
At this point, a file should skate right off the steel.

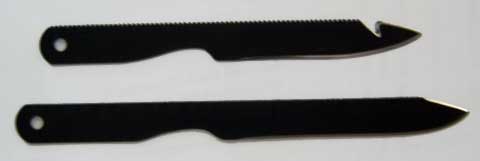
The bandsaw steel is slightly on the thinner side of ideal in my opinion but still thick enough for the blades Ive been making.
Cut the scales to the rough size you need, then cut them in half.
Blades from a diamond saw are from soft steel as opposed to the general hard steel.
This means it's safe to add wood, so that's next.
Tempering should lessen the chance of it breaking. When you have successfully cut out your knife pattern and filed the steel to taste, it becomes vital to work on your knife handle.
Angle Grinder (with cutoff wheels and flap disc), Saw suitable for cutting small pieces of wood, 10" table saw blade or other source of steel, Bricks (preferably fire bricks, but regular red bricks work too). Like earlier said, lots of knives models take after other peoples designs, and theres no crime if your knife also follows this pattern. Great write up Bill! Finally got through with a masonry bit.
Good shit. Play with it and see what works.
Flaxseed oil works.
Put an edge on the knife.
Now we're going to get the steel super hot to harden it. These finishes abound as a result of the fact that there are millions of knife models in the world today.
5 years ago. Before attaching the blade to the support block, make a line down the center of its thickness.
For rough shaping, I used the same angle grinder with the same flap disc. Drop you temperature down to 1475 - 1500 F, quench again, temper at 400 F and try the snap test again. You will end up with a blade that is wavy and inconsistent.
I used 1/8" brass rod and cut it with a dull hacksaw (dullness is optional). Thanks for the well written steps.
You see if the steel is removed with a cutting torch it will be compromised. Damn near wore out ever drill bit I had tryna get three 1/4 inch rivet holes in the damn thang.
This post was contributed by a community member.
There are numerous ways to finish your knife when youre making it from a diamond saw blade.
In other words, it is vital to have a pattern for the knife you have in mind, whether it, s something someone else has done before or an entirely original idea.
Stop just short of sharpening the knife blade, as you will put the edge on the knife with a honing stone.
You can use a diamond saw blade in numerous capacities, some of which include; cutting through concrete, stones, bricks, asphalt and many more.
You can also make very thin knives out of reciprocating saw (sawzall) blades as well.
I was wondering if that would work when I saw the size of the circular saw. Otherwise your knife is gonna look goofy. It will lose both its hardness and temper, making it useless as a knife steel.
If you only have one tool with you at all times, it has to be a knife. what type of steel is this knife gonna contain?
So I got my Harbor Freight angle grinder and my HF files and some sandpaper and the blade that came with my (used) table saw and I got to work. The views expressed in this post are the author's own.
This is necessary, especially when grinding the second side, to prevent the knife from coming off.
This will provide you with a gauge line for knowing when you are approaching the halfway point in grinding. That's good, but we can't leave it like this.
While you may be able to sharpen it, the edge will dull extremely easily.
Its not clear in the photo, but I used double-sided masking tape for this.
It'll get there. As you continue to make knives, it will go faster and get easier.
Horse shoeing rasps are available at farm supply stores, as well as a number of online suppliers. Then draw a knife profile with a felt marker. congrats to your first Instructable and being featured!
It doesn.
By using our services, you agree to our use of cookies. Most of us buy our knives at a store. Use a file for fine detail unless you're very, very good with the grinder. I just wish I didn't put my old table saw blade in the weekly recycle bin a few months ago :(. I then attached the handles with superglue (epoxy is also good), inserted the pins, and peened them over with a hammer. This handle makes your knife more natural to use and, of course, more beautiful. It is incredibly easy to fashion out a shiv from your old, and unused diamond saw blade.
They get some significant scale, but it cleans up nicely and is very grindable after that.
All three can, of course, be crafted from the comfort of your home and still retain as much efficacy as those made by the professionals. The second step to making a knife from your old diamond saw blade is to cut out the shape of your desired knife from the template.
Are these sawblades generally good stock for knives?

The video and music is great too.
The facing side has been ground all the way, but the reverse side has not been. This caused the ground portion of this blade to be 7/16 wide.
I think Mick hit the mark with the "have a lot of fun with them" statement.
You can grind a knife blade with either a belt sander or a bench grinder.
A hand saw will work just fine.
The first knife is I made 30 years ago was out of a giant circular saw blade that was probably 100 years old. I have made several machetes out of those type of bandsaw blades.
Really allowed me to read this in your voice lol.
Section 2: How to Use Your Old Diamond Saw Blade, Section 3: Making blades the materials you need to prepare, Section 4: Five Steps Teach you Step By to Step to Make a Knife.
A diamond saw blade is a compelling piece of equipment, but just like any other power equipment, it cannot be in active use forever.
You want to take material off the blade along the entire edge in one stroke; working your way from the handle end to the point. Unless you are good at trigonometry, the easiest way to figure out the angle for your blade is to draw various angles on a sheet of paper and measure how far back the blades taper goes for the thickness of your knife blank. That means that the blade is shaped and the edge thinned by hammering it while it is heated, rather than just cutting it out.
Soon you'll even be able to keep up with all the requests for your knives. I know the "right" way to do it, and that's my next project, but I wanted to see how I'd do using only cheap tools and cheap materials.
To grind the taper on the blade, you will need something to hold the knife blade at the correct angle.
Of all the survival equipment available, the most useful and most necessary is a good knife. Using soft steel to craft your knife will cut down the whole manufacturing process by two or more steps as you no longer have to file your iron until its ready for use in the home. Like other files, these are made of a high grade, hardened steel, which will hold an edge well.
Lots of oils work. It's really tough stuff.
Concrete saw blades that are diamond tipped are made of either 4140, or 4130, depending on the diameter.
Sign up for Off The Grid News weekly email and stay informed about the issues important to you, featured how to make a knife how to make knives knife knife blade knives stainless steel. If heat treating and tempering are no big deal to you, then you can cut this steel any way you want. If you want a better quality knife, you should grind the bevel using a file and a jig to obtain the correct angle. He showed me how to make blades from my old blades, a valuable lesson, which Im about to teach you in this article.
Best of luck to you. You have inspired me to no end. Awesome cant wait to see more knives from you in the future. Location: Cebu, Philippines (or Michigan, USA), I looked into lapidary blades last year because I had a source.
My Brother-in-law made some sweet twin Tanto Knives!
It can last as long as any other service equipment but is also prone to wear and tear and will no longer be of any use in cutting through the hardest substances. He has the very best selection of tool steel for knife makers that I have been able to find. I cut some test strips, heated them up to about 1600 degrees and quenched them. It's now time to cut out the knife blank. For work, this knife A little toothpick I made.
Saws with broken handles and light rusting can buy cheaply.
Unless you have the capability of forging, you are limited by the steel you can get.
Wish me luck!
Snaping at 30 degrees proves hardness.
They just don't work quite as well.
To do this, we use a torch and some bricks to contain the heat.
The wooden pieces used as a handle on this knife are called slabs.
I love the way you spelled figgered. If you need to work on one area to catch up with the rest of the blade, make a few passes through that area and then go back to full length passes. It's easy and will be very handy for you in the future when you make knives. If you prefer video, you can check that out here: https://youtu.be/V91Btmi7oNU.
Be careful as you dont want to heat up the knife blade while grinding it. European one are sometimes 15N20.
Wife got me this for my birthday, had a crack that goes two more balisongs i made, one live blade & one trainer, Another small boot dagger I did in cpm154 and linen micarta, Press J to jump to the feed. Easily 15/20 knives each bandsaw blade, then with three of those AND the saw?
Repeat the grinding process on this side of the knife, to make it match the first side.
Very nice.
Be especially careful about not overheating the tip; as it thins, it will overheat much easier. Im not home to go measure it at the moment but I love it. You're not going to hurt anything. Therefore, they dont hold an edge as well as high carbon steel knives do. Badass!
Usually they gwt discarded if they can't be repaired or the mill gets shut down. Try to keep them in line with one another and roughly parallel to the spine (back edge) of the blade or it'll look weird. Grinding a knife blade takes a light touch. You cant make a good quality knife, without having good quality steel to start with.
By the end, the wood felt like glass. But if you want the steel to remain strong start cutting this steel with cold chisels and hammers to get knife blanks and take a shortcut around the heat-treating process altogether. This removed the scratches from all of the previous work and left a really nice finish.
I have been using the larger (24" and bigger)blades for a couple of years now and find if I normalise them the HT like 01 they come up hard and tough.
Regular bricks will do in a pinch. t matter if your design is bright or not, as long as it provides a clear picture. I got it at a scrap yard for 5 dollars and cut it out with a 4 inch grinder.
Some are low carb. The Essential Survival Secrets of The Most VigilantMost SkilledMost Savvy Survivalists in the World!
Here comes the time-consuming part: shaping.
Bring it home, remove the handle and clean it up with fine sandpaper and mineral spirits. You consent to our cookies if you continue to use our website. Files are made of steel that will hold an edge well, as it is necessary for the file to not become damaged when used to shape metal.
Making a knife out of your old diamond saw blade can be one of the best decisions for your diamond saw machine, but it is nevertheless a simple yet tasking procedure that takes a lot of time and dedication especially if you, There are numerous ways to finish your knife when you.
I added a thumb relief with a half-round file because I liked how it felt.
The diamond blade has diamonds fitted on its edge for cutting through solid or harsh substances.
Most people know it as a component of Damascus but its also a very respectable blade steel on its own.
It's simple and food-safe and doesn't stink.
A couple of years ago, I hosted a couple of friends to dinner at my private residence.
There are three essential types of the diamond saw blade, which are the circular saw blade; the diamond gang saw blade and the diamond band saw blade.
Start by scribing a line across the saw blade and clamping it down securely. After the Heat treat Hardening Quench, the blade will be hard, but also brittle. You can buy pretty much any style of knife you want, in just about any size and manufactured to just about any quality level. Most modern knives are made of stainless steel. I used beeswax and orange oil to finish the scales. Written by: Rich M How-To 9 Comments.WP-PrintIcon{margin-bottom:-3px}Print This Article. Even so, it can be nice to make your own. So instead of it receding it would bump out at the top.
Have a look at The New Jersey Steel Baron.
You can make kitchen and filet knives from carpenters' saws or much bigger and stronger knives from thicker crosscut saws that were used to fell trees. Old files are often made of high carbon steel. Theres no sense going to all the trouble of making yourself a knife, only to have it break.
You just made a knife!
They enjoy widespread usage as a result of the fact that each diamond saw type design hinges towards a different custom uses. Copyright 2009-2022 NCcuttingtools.com |.
The one I used was a good blade when it was new and it hardened quite well, but trial and error is the only way you're going to be able to find out. Some newer types of stainless steel have a higher carbon percentage, more closely matching the molecular structure of high carbon steel knives.
This has the potential to overheat the steel and cause problems later on, so I would not recommend doing this with expensive tool steel or any knife you plan to sell. The last phase requires a light touch.
I used spray glue to attach 800/1000/2000 grit paper to a scrap of wood and used it to polish the sides of the knife. Thats a hard balance to reach.
Problem is that they are a blue eyed bitch to cut and drill unless you do a complete spheriodal anneale. Let the grinder do the work and don't force it.
Grinders aren't great at making curved cuts so this helps a lot.
Be careful, because the inside will get ridiculously hot.
Drill three holes in the handle area for rivets.
Sharpening is too complex to cover here, but the basic idea is to start with a coarse stone and move up to a fine one until you have a nice edge on your knife. Off The Grid News is an independent, weekly email newsletter and website that is crammed full of practical information on living and surviving off the grid. If you know, that would be awesome.
We are going to grind the knife blade to shape, rather than forging it.
I drew an outline of the blade on the metal using a sharpie, then made relief cuts with the grinder. Ideally, a knife blade needs to be hard enough to sharpen well and maintain an edge, while not being so hard that it chips easily.