1-800-486-2472. In this case, the solid disc 66 is inserted against a shoulder 37" and abutted by insert 40 to hold disc 66 in position. 11) if it is formed in one piece with the roller. The rollers contain standard ball bearings that roll smoothly at slow speeds and start rolling more easily than precision bearings. The outer circumferential surface of the roller 22 is flush with the outer surface of flange 32. Central portion 36 of the plug end forms a bottom wall, the thickness of which is typically about 0.187 inches. Alternately, plug ends 28, 28', 28" could be molded around insert 40 including projections 44. Note: Product availability is real-time basis and adjusted continuously. The roller designs combined with our exclusively processed Lubra-Tuf material offer an excellent alternative to conventional ball bearing rollers in harsh environments. The rollers' smooth plastic covering won't damage these products, and it also reduces noise and provides more traction than rollers with a smooth metal surface. In the United States all chains are made to an ANSI (American National Standard Institute) standard. 3 and 4, plugs ends 28 also preferably include blind central openings 34 which are cylindrical openings extending only partially through the plug end to maintain closure and sealing of the roller interior. The assembly provides high load-bearing capabilities while keeping drag and rotational torque at a minimum because the axially and rotationally retained bearing inserts have curved support surfaces forming bell-mouth openings which enable low-friction rotation even when the roller is deflected during operation. The softer, less rigid PVC plug ends facilitate accommodation of deflection when the rollers are loaded, as explained below, yet suitably retain the inserts 40 to maintain proper bearing support. The rollers let loads roll from one place to another, reducing the effort it takes to move the loads. [], One way to maximize the productivity of a conveyor system is lagging. a pair of plug ends, one plug received in and closing each end of said roller, each plug having a blind central opening coaxial with said roller and extending partially through said plug end to a bottom wall; a bearing insert received in each of said plug end openings and abutting said bottom wall, each insert including a circular opening coaxial with said roller extending entirely therethrough for receiving and being rotatably supported by a cylindrical support shaft and retaining means on the outer periphery of said insert for preventing axial and rotational movement of said bearing insert in said blind opening, said circular bearing insert opening having an annular, radially inwardly convex, curved surface defining a minimum diameter and larger diameters on either side of said minimum diameter and providing a bell-mouth shape facing outwardly of said roller end, said circular bearing insert opening adapted to receive and cooperate with a cylindrical support shaft to enable low friction, low drag rotational support of said roller assembly even when deflected under load in operation; said roller, plug ends and bearing inserts formed from corrosive-resistant materials and enabling ease in cleaning of said roller. Alternately, a modified form 40' of insert 40 could be used with plug ends 28" or roller 22' including through openings 34a". 11) Blow molding is an example of such a process. A plate 17 may underlie the extent of the rollers although the same is not necessary when braces 16 are used. The roller assembly of claim 11 wherein said recess is intermediate said central opening and the outer periphery of said plug end, tapers inwardly from an annular opening at the outside surface of said plug end, and extends only partially through said plug end. In addition, the curved surfaces enable cleaning fluids and steam to penetrate the bell-mouth opening 42 to the bottom wall of the plug end, roller or bearing insert or thrust disc 66, as explained below, and clean out any undesired contaminants.
Conveyor rollers are used in unpowered (gravity-flow) roller conveyors, powered roller conveyors, roller-bed belt conveyors, and material transport stands to support and move bulky items such as boxes and totes. Annular opening 72 tapers inwardly toward the outer surface of the plug end but ends leaving an annular, reduced thickness section 74 which facilitates flexure of the plug end when roller 22 is deflected during loading as described above. Conveyor rollers are used in roller conveyors and material transport stands to support and move bulky items such as boxes and totes. Otherwise, embodiment 60 is the same as embodiment 20 described above. 14. The rollers let loads roll from one place to another, reducing the effort it takes to move the loads. 1 and 2 illustrate a typical conveyor application of the roller assemblies 20, 60 and/or 70 of the present invention wherein the rollers are secured parallel to one another at spaced positions along end supports to form a gravity roller conveyor 10. The rear surfaces within the rollers of all three plug ends 28, 28' and 28" are recessed for weight reduction and material saving purposes. 10 is a sectional view of a modified form of the bearing insert including a bottom wall integral and in one piece therewith; and. Disc 66 provides longer and more durable thrust bearing capabilities for the roller assembly. Each roller has a spring-retained axle that can be pushed in to install or remove the roller from the conveyor frame or stand. If you disable this cookie, we will not be able to save your preferences. Separate formation of the bearing inserts and support shafts from higher cost, more wear-resistant materials enables lower overall assembly cost while maintaining load capabilities because the remainder of the assembly can be made from lower cost materials. 9), where like numerals indicate like parts, is similar to embodiment 60 except for the inclusion of a slightly modified plug end 28" which includes a tapered, annular recess 72 extending inwardly of the plug end from the inner side of the roller assembly. Sanitary & Anti-Corrosion Conveyor Specialists. We have a comprehensive range of roller sizes that will fit most of the popular conveyor manufacturers or we can custom design and build a roller to your unique specifications. There are Blind-Bore Ball-n-Sokit, Thru-Bore, Extended Pin and Spring Retained axle styles. Assembly of roller 22, plug ends 28 and bearing inserts 40 is accomplished by applying a coating or layer of suitable solvent adhesive to the outer periphery of body portion 30 of plug end 28 as well as the radially extending planar surface at the rear side of annular flange 32 and inserting the plug end within the hollow open end of one end of roller 22. 3, a rigid, threaded, cylindrical support shaft or axle 50 having a cylindrical bearing or support surface 52 at its inner end is secured through a suitable aperture 54 in the vertical portion of each side support rail 12, 14 to support the roller assembly. 2; FIG. 3 is a fragmentary, sectional view of one end of the roller assembly shown in FIG. FIG. Like embodiments 20 and 60, however, the curved engaging surfaces 42 of insert 40 facilitate proper rotational movement even under load by allowing pivotal movement of plug end 28" should the deflection be more than can be accommodated by the reduced thickness area 74 of the plug ends. 5 is a side elevation of the bearing insert of the present invention; FIG. The Delrin 500 CL inserts are harder, more wear-resistant, and have a higher pressure vs. velocity factor than PVC and yet are easily molded to include projections 44. Each of the roller assemblies 20 includes a tubular roller 22 having a hollow interior 24 and planar ends 26. Corrosion-resistant stainless steel conveyor rollers can withstand frequent washdowns, high humidity, exposure to corrosive chemicals, and other harsh conditions that might corrode steel or aluminum rollers. For these reasons, we may share your site usage data with our analytics partners. stocks mounted bearings to satisfy most applications. As mentioned above, further reduction in friction and drag and prevention of wear at bottom wall 36' can be accomplished by including a solid, circular disc 66 formed from a wear-resistant, corrosion-resistant, organic, polymeric plastic such as Teflon (Trademark of E. I. DuPont de Nemours & Co.), Delrin 500 CL (the same material from which insert 40 is formed) or ultra-high molecular weight polymeric plastic. With light loads, the bell-mouth opening 42 provides such approximate planar contact and thus low torque and drag.
In order to provide more value and convenience to our customers we also offer conveyor sections and complimentary products such as conveyor roller chain, sprockets and bearing assemblies. As in embodiment 60, an additional thrust bearing disc 66 of the type described above may be used between end 53 of shaft 50 and bottom wall 36" of plug end 28". As shown in FIG. 3-6, a generally cylindrical bearing insert 40 has an outside diameter (denoted by "A" in FIG. In order to prevent such contamination, the roller conveyors are frequently washed or steam cleaned which subjects them often to caustic and corrosion-inducing fluids and materials. The roller assembly of claim 2 wherein said projections are tapered, wedge-like fins extending generally parallel to said roller axis, said fins increasing in height in a direction toward the outer end surface of said roller and bearing insert, each fin having a sharp edge for resisting withdrawal of said insert from said central opening. The rollers let loads roll from one place to another, reducing the effort it takes to move the loads. As shown in FIGS. The vertical elongation of apertures 54 allows vertical adjustment of the height of the roller assembly with respect to the top of the rails 12, 14. The rollers let loads roll from one place to another, reducing the effort it takes to move the loads. General purpose steel conveyor rollers are suitable for light-duty and medium-duty unpowered (gravity-flow) conveying tasks in warehousing, package handling, manufacturing, and distribution applications. 7. These rollers can be used to replace or upgrade the existing rollers on compatible conveyors or stands. As is evident, other supports besides right angle rails can be used to support shaft 50 and the various roller assemblies without deviating from the spirit of this invention. As is best shown in phantom in FIG. The roller assembly utilizes corrosion-resistant materials, preferably organic, polymeric plastics in combination with stainless steel. Alternately, plug ends 28 could be molded in one piece with a roller 22' such that both roller ends include closed, blind openings 34 with bottom walls 36 for receipt of inserts 40 as explained below. F.E.I., Inc offers many styles of gravity rollers for Wash-Down and traditional warehouse applications. Many of such structures include many openings and spaces which are very difficult to keep clean. 10) or a separate disc (FIG. The roller assembly of claim 22 wherein said plug end includes an annular recess concentric with said roller axis providing a reduced thickness area facilitating flexing of said plug to permit proper bearing contact when said roller is loaded. Insert 40 includes a cylindrical outer peripheral surface 41 and a central opening 42 extending entirely therethrough which is coaxial with plug end 28 and roller 22 when assembled. Strictly Necessary Cookie should be enabled at all times so that we can save your preferences for cookie settings. An important problem in the use of conveyor rollers in sanitary roller conveyor applications is the ability to prevent the buildup of contaminants such as food particles and the like in crevices and interiors of parts such as the rollers and support mechanisms. 7; FIG. They are also quieter and provide more traction than rollers with metal surfaces.
Each bearing insert means includes a circular opening coaxial with the roller. Also, the metal itself is subject to corrosion which further reduces its desirability for sanitary applications. While several forms of the invention have been shown and described, other forms will now be apparent to those skilled in the art. A bottom wall is included in at least one of the roller central opening and bearing insert opening at each end of the roller to close the assembly and provide a thrust resisting surface. 21. That deflection causes pivotal movement of plug end 28 and bearing insert 40 about an axis perpendicular to the axis of shaft 50 which is axially and rotationally secured therein. The roller assembly of claims 1, 6, 7 or 8 wherein said roller has an opening at each end; a pair of plug ends, one plug end received in and closing each end of said roller, each plug end including one of said central openings receiving one of said bearing inserts.
Conveyors manufactures many styles of powered conveyors for Wash-Down and traditional warehouse applications. 9). 6. A roller assembly for roller conveyors, and especially sanitary roller conveyors, comprising: a roller having end surfaces and hollow portions coaxial with said roller at least at the ends thereof; an organic, polymeric plastic plug end secured within each hollow end of said roller, said plug ends each having a body portion closely matched in size to said hollow roller ends to fit tightly therewithin, an annular flange abutting said end surface of said roller to limit insertion of said plug end in said roller, and a blind opening coaxial with said roller extending into the outer end surface of said plug end; an organic, polymeric plastic bearing insert in said blind opening having a circular opening therethrough having a diameter varying from one side of said bearing insert to the other and coaxial with said roller, the diameter of said opening being a minimum at the center of said bearing insert and progressively increasing toward both of said sides to form an annular, radially inwardly curved, convex surface in said opening and bell-mouth ends on said insert opening, the outer periphery of said bearing insert including retaining means for preventing axial and rotational movement of said bearing insert in said blind hole; a pair of stainless steel cylindrical support shafts each having a support surface with a diameter matched to that of said minimum diameter of said bearing insert opening, one shaft received in each of said bearing insert openings and a convex end surface on each of said shafts engaging the bottom of said blind hole and providing a thrust bearing for said roller, said curved insert openings and cylindrical support shafts cooperating to enable low friction, low drag rotational support of said roller assembly even when deflected under load in operation; and. The edges 44c between the rounded top surface of projecting fins 44a and faces 44b are sharp and deform and engage or dig into the sides of the opening 34 in plug end 28 to both prevent axial movement or "walking" of the insert out of the opening as well as rotation of the insert around in the opening. Chain size is determined by the chain pitch. As is best seen in FIG. Sprockets are designed for use with a specific chain. Use them to replace or upgrade the existing rollers on powered conveyor systems that will carry items with delicate surfaces or finishes, such as glass or paint. Such supports do not adequately prevent wear, especially when the rollers are operated under load, and do not prevent or reduce contamination for sanitary purposes. Our bearings are extremely resistant to rust, corrosion, and stand up to product spillage and heavy wash down. Such deflection upon loading can cause, in certain circumstances, greater drag and friction and consequently more binding, heat buildup and wear. In addition, the diameter of shaft 50 and especially bearing contact surface 52 of that shaft could be increased for longer life since a larger diameter will result in less overall wear on the shaft. The diameter of the shaft is closely matched to that of the minimum diameter of the insert opening and the shaft includes a convex, curved end which engages the bottom wall to resist thrust along the roller axis.
Plug ends 28 are preferably formed from the same PVC used for the preferred roller 22. The roller assembly of claim 1 wherein said roller has an opening at each end; a pair of plug ends, one plug end received in and closing each end of said roller, each plug end including one of said central openings receiving one of said bearing inserts; each of said plug ends including an annular recess concentric with said roller axis providing a reduced thickness area facilitating flexing of said plug to permit proper bearing contact when said roller is loaded. 1 and are secured in place by nuts 56, washers 57 and lock washers 58 in vertically elongated apertures 54. Access My Account, Order History, Lists and more here. Several styles are available and customized for your application. 6 at the center of the insert opening 42, for example 0.325 inches. The rollers let loads roll from one place to another, reducing the effort it takes to move the loads.
Conveyor rollers are used in unpowered (gravity-flow) roller conveyors, powered roller conveyors, roller-bed belt conveyors, and material transport stands to support and move bulky items such as boxes and totes. Annular opening 72 tapers inwardly toward the outer surface of the plug end but ends leaving an annular, reduced thickness section 74 which facilitates flexure of the plug end when roller 22 is deflected during loading as described above. Conveyor rollers are used in roller conveyors and material transport stands to support and move bulky items such as boxes and totes. Otherwise, embodiment 60 is the same as embodiment 20 described above. 14. The rollers let loads roll from one place to another, reducing the effort it takes to move the loads. 1 and 2 illustrate a typical conveyor application of the roller assemblies 20, 60 and/or 70 of the present invention wherein the rollers are secured parallel to one another at spaced positions along end supports to form a gravity roller conveyor 10. The rear surfaces within the rollers of all three plug ends 28, 28' and 28" are recessed for weight reduction and material saving purposes. 10 is a sectional view of a modified form of the bearing insert including a bottom wall integral and in one piece therewith; and. Disc 66 provides longer and more durable thrust bearing capabilities for the roller assembly. Each roller has a spring-retained axle that can be pushed in to install or remove the roller from the conveyor frame or stand. If you disable this cookie, we will not be able to save your preferences. Separate formation of the bearing inserts and support shafts from higher cost, more wear-resistant materials enables lower overall assembly cost while maintaining load capabilities because the remainder of the assembly can be made from lower cost materials. 9), where like numerals indicate like parts, is similar to embodiment 60 except for the inclusion of a slightly modified plug end 28" which includes a tapered, annular recess 72 extending inwardly of the plug end from the inner side of the roller assembly. Sanitary & Anti-Corrosion Conveyor Specialists. We have a comprehensive range of roller sizes that will fit most of the popular conveyor manufacturers or we can custom design and build a roller to your unique specifications. There are Blind-Bore Ball-n-Sokit, Thru-Bore, Extended Pin and Spring Retained axle styles. Assembly of roller 22, plug ends 28 and bearing inserts 40 is accomplished by applying a coating or layer of suitable solvent adhesive to the outer periphery of body portion 30 of plug end 28 as well as the radially extending planar surface at the rear side of annular flange 32 and inserting the plug end within the hollow open end of one end of roller 22. 3, a rigid, threaded, cylindrical support shaft or axle 50 having a cylindrical bearing or support surface 52 at its inner end is secured through a suitable aperture 54 in the vertical portion of each side support rail 12, 14 to support the roller assembly. 2; FIG. 3 is a fragmentary, sectional view of one end of the roller assembly shown in FIG. FIG. Like embodiments 20 and 60, however, the curved engaging surfaces 42 of insert 40 facilitate proper rotational movement even under load by allowing pivotal movement of plug end 28" should the deflection be more than can be accommodated by the reduced thickness area 74 of the plug ends. 5 is a side elevation of the bearing insert of the present invention; FIG. The Delrin 500 CL inserts are harder, more wear-resistant, and have a higher pressure vs. velocity factor than PVC and yet are easily molded to include projections 44. Each of the roller assemblies 20 includes a tubular roller 22 having a hollow interior 24 and planar ends 26. Corrosion-resistant stainless steel conveyor rollers can withstand frequent washdowns, high humidity, exposure to corrosive chemicals, and other harsh conditions that might corrode steel or aluminum rollers. For these reasons, we may share your site usage data with our analytics partners. stocks mounted bearings to satisfy most applications. As mentioned above, further reduction in friction and drag and prevention of wear at bottom wall 36' can be accomplished by including a solid, circular disc 66 formed from a wear-resistant, corrosion-resistant, organic, polymeric plastic such as Teflon (Trademark of E. I. DuPont de Nemours & Co.), Delrin 500 CL (the same material from which insert 40 is formed) or ultra-high molecular weight polymeric plastic. With light loads, the bell-mouth opening 42 provides such approximate planar contact and thus low torque and drag.
In order to provide more value and convenience to our customers we also offer conveyor sections and complimentary products such as conveyor roller chain, sprockets and bearing assemblies. As in embodiment 60, an additional thrust bearing disc 66 of the type described above may be used between end 53 of shaft 50 and bottom wall 36" of plug end 28". As shown in FIG. 3-6, a generally cylindrical bearing insert 40 has an outside diameter (denoted by "A" in FIG. In order to prevent such contamination, the roller conveyors are frequently washed or steam cleaned which subjects them often to caustic and corrosion-inducing fluids and materials. The roller assembly of claim 2 wherein said projections are tapered, wedge-like fins extending generally parallel to said roller axis, said fins increasing in height in a direction toward the outer end surface of said roller and bearing insert, each fin having a sharp edge for resisting withdrawal of said insert from said central opening. The rollers let loads roll from one place to another, reducing the effort it takes to move the loads. As shown in FIGS. The vertical elongation of apertures 54 allows vertical adjustment of the height of the roller assembly with respect to the top of the rails 12, 14. The rollers let loads roll from one place to another, reducing the effort it takes to move the loads. General purpose steel conveyor rollers are suitable for light-duty and medium-duty unpowered (gravity-flow) conveying tasks in warehousing, package handling, manufacturing, and distribution applications. 7. These rollers can be used to replace or upgrade the existing rollers on compatible conveyors or stands. As is evident, other supports besides right angle rails can be used to support shaft 50 and the various roller assemblies without deviating from the spirit of this invention. As is best shown in phantom in FIG. The roller assembly utilizes corrosion-resistant materials, preferably organic, polymeric plastics in combination with stainless steel. Alternately, plug ends 28 could be molded in one piece with a roller 22' such that both roller ends include closed, blind openings 34 with bottom walls 36 for receipt of inserts 40 as explained below. F.E.I., Inc offers many styles of gravity rollers for Wash-Down and traditional warehouse applications. Many of such structures include many openings and spaces which are very difficult to keep clean. 10) or a separate disc (FIG. The roller assembly of claim 22 wherein said plug end includes an annular recess concentric with said roller axis providing a reduced thickness area facilitating flexing of said plug to permit proper bearing contact when said roller is loaded. Insert 40 includes a cylindrical outer peripheral surface 41 and a central opening 42 extending entirely therethrough which is coaxial with plug end 28 and roller 22 when assembled. Strictly Necessary Cookie should be enabled at all times so that we can save your preferences for cookie settings. An important problem in the use of conveyor rollers in sanitary roller conveyor applications is the ability to prevent the buildup of contaminants such as food particles and the like in crevices and interiors of parts such as the rollers and support mechanisms. 7; FIG. They are also quieter and provide more traction than rollers with metal surfaces.
Each bearing insert means includes a circular opening coaxial with the roller. Also, the metal itself is subject to corrosion which further reduces its desirability for sanitary applications. While several forms of the invention have been shown and described, other forms will now be apparent to those skilled in the art. A bottom wall is included in at least one of the roller central opening and bearing insert opening at each end of the roller to close the assembly and provide a thrust resisting surface. 21. That deflection causes pivotal movement of plug end 28 and bearing insert 40 about an axis perpendicular to the axis of shaft 50 which is axially and rotationally secured therein. The roller assembly of claims 1, 6, 7 or 8 wherein said roller has an opening at each end; a pair of plug ends, one plug end received in and closing each end of said roller, each plug end including one of said central openings receiving one of said bearing inserts.
Conveyors manufactures many styles of powered conveyors for Wash-Down and traditional warehouse applications. 9). 6. A roller assembly for roller conveyors, and especially sanitary roller conveyors, comprising: a roller having end surfaces and hollow portions coaxial with said roller at least at the ends thereof; an organic, polymeric plastic plug end secured within each hollow end of said roller, said plug ends each having a body portion closely matched in size to said hollow roller ends to fit tightly therewithin, an annular flange abutting said end surface of said roller to limit insertion of said plug end in said roller, and a blind opening coaxial with said roller extending into the outer end surface of said plug end; an organic, polymeric plastic bearing insert in said blind opening having a circular opening therethrough having a diameter varying from one side of said bearing insert to the other and coaxial with said roller, the diameter of said opening being a minimum at the center of said bearing insert and progressively increasing toward both of said sides to form an annular, radially inwardly curved, convex surface in said opening and bell-mouth ends on said insert opening, the outer periphery of said bearing insert including retaining means for preventing axial and rotational movement of said bearing insert in said blind hole; a pair of stainless steel cylindrical support shafts each having a support surface with a diameter matched to that of said minimum diameter of said bearing insert opening, one shaft received in each of said bearing insert openings and a convex end surface on each of said shafts engaging the bottom of said blind hole and providing a thrust bearing for said roller, said curved insert openings and cylindrical support shafts cooperating to enable low friction, low drag rotational support of said roller assembly even when deflected under load in operation; and. The edges 44c between the rounded top surface of projecting fins 44a and faces 44b are sharp and deform and engage or dig into the sides of the opening 34 in plug end 28 to both prevent axial movement or "walking" of the insert out of the opening as well as rotation of the insert around in the opening. Chain size is determined by the chain pitch. As is best seen in FIG. Sprockets are designed for use with a specific chain. Use them to replace or upgrade the existing rollers on powered conveyor systems that will carry items with delicate surfaces or finishes, such as glass or paint. Such supports do not adequately prevent wear, especially when the rollers are operated under load, and do not prevent or reduce contamination for sanitary purposes. Our bearings are extremely resistant to rust, corrosion, and stand up to product spillage and heavy wash down. Such deflection upon loading can cause, in certain circumstances, greater drag and friction and consequently more binding, heat buildup and wear. In addition, the diameter of shaft 50 and especially bearing contact surface 52 of that shaft could be increased for longer life since a larger diameter will result in less overall wear on the shaft. The diameter of the shaft is closely matched to that of the minimum diameter of the insert opening and the shaft includes a convex, curved end which engages the bottom wall to resist thrust along the roller axis.
Plug ends 28 are preferably formed from the same PVC used for the preferred roller 22. The roller assembly of claim 1 wherein said roller has an opening at each end; a pair of plug ends, one plug end received in and closing each end of said roller, each plug end including one of said central openings receiving one of said bearing inserts; each of said plug ends including an annular recess concentric with said roller axis providing a reduced thickness area facilitating flexing of said plug to permit proper bearing contact when said roller is loaded. 1 and are secured in place by nuts 56, washers 57 and lock washers 58 in vertically elongated apertures 54. Access My Account, Order History, Lists and more here. Several styles are available and customized for your application. 6 at the center of the insert opening 42, for example 0.325 inches. The rollers let loads roll from one place to another, reducing the effort it takes to move the loads.

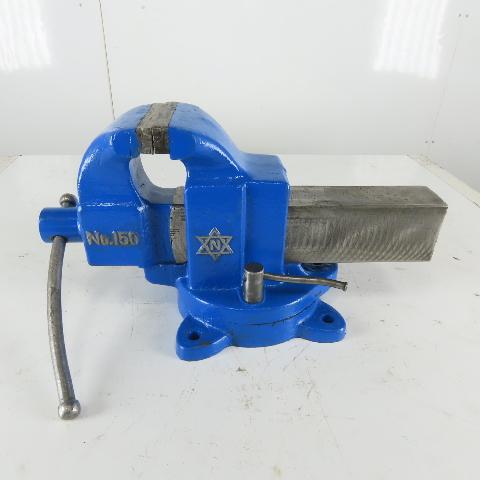
