The difference between normal steel and galvanized steel is the presence of the zinc layer that makes it rust-resistant.
Q: what were the machine and amperage settings for this weld repair? The 3xx.0 series, including 356.0, 357.0, and 319.0 aluminum casting, are treatable by heat and can also be welded as base materials with aluminum filler alloy 4043. To provide well-researched and informative articles. These include 356.0, 357.0, and 319.0, which are aluminum-silicon-magnesium alloys. However, the level of weldability depends on many factors. These are actually not heat-treatable but are also readily weldable with the help of a 5356 filler rod. ac balance set to 35% cleaning, ac frequency set to 80hz, using a #6 cup with around 15 cfh argon. There are many casting processes, including green sand casting, investment casting, permanent mold casting, and die casting, just to name a few. Read More What Are The Different Types of Welding Joints?Continue, Read More Best Time of Year to Buy a Generator?Continue, Read More How to Bond Metal Without WeldingContinue, Read More Can A 2000 Watt Generator Run A Refrigerator?Continue. It moves fast, and it needs a mechanical feeding system with a spool gun or push-pull gun for feeding to happen. More filler was added to these isolated areas, then the affected areas were "washed in." Welding heat-treated castings reduce the tensile properties of the material. Copy and paste it, adding a note of your own, into your blog, a Web page, forums, a blog comment, 4047 usually gets less porosity so that can help on things like polished crankcases. These are not heat-treatable but are readily weldable using 5356 filler. Q:Are you going to fabtech this year in Vegas? This process uses 100% argon as a protective gas, and it doesnt require a mechanical wire feeding. Taking into consideration the nature of aluminum that is also susceptible to cracking. More about that in a minute. Aluminum casts are still aluminum, but you never know which type of aluminum alloy or even other types of metal the manufacturer used to create it. Sand castings, investment castings, and permanent mold castings are usually very weldable because molten aluminum is cast into a mold that is a relatively poor thermal conductor, so the casting solidifies slowly. The process prevents any gases from escaping, resulting in gas pockets in the casting. Impurities from lubricants, dirt, and coolant can build up on the rough cast surface and cause defects in the weld. Brazing Aluminum Methods and Steps How to Braze Aluminum? The worst cast aluminum weld repairs are usually due to oil or exhaust gas carbon.or a blend of the 2. Ensure that your push-pull feeding wire is set and ready to work.
But if you still decide to do it, using a 250amp TA welder with an HTP spool gun is a good way to start. However, each of them involves proper preparation as the main factor. Super Alloy 1 comes in 1/8 and 3/32 diameter, while Super Alloy 5, the one that we need, goes between 1/16 and 3/32 diameter. Grinding with a die grinder should also be considered as part of preparation. It can be flimsy and touchy to do, but it can be done with proper preparation. Since MIG welding cast aluminum is the hardest choice, a 250amp TA welder is what we recommend, but only if you really have to. Some of the more notable ones include die casting, investment casting, permanent mold casting, or green sand casting. Tig welding aluminum is often the preferred method. TIG welding to the rescue! in diameter on the inner and outer surfaces. Some TIG welds can be done without adding fillerthese are called autogenous, and essentially fuse the two halves of the workpiece with the material that's already there. However, die castings are very different. Due to the porosity of our cast aluminum, we used the 4043 silicon alloy, which is superior at mitigating porosity and oxidation in the affected weld area. By contrast, this form of welding involves passing an electrical current through the parts that are to be joined together while applying pressure. The gas can come from lubricants, abrasive grit, moisture, hydrogen, oxides, etc. There are a few ways that welders use to weld aluminum castings. When the arc forms, the electrode melts and becomes part of the weld. Actually, some of them are considered completely unweldable. Note that the torch faces in the direction of weld movement to keep the weld enveloped by the shielding gas. Also, be sure not to weld anything until all the chemicals have evaporated. In the case of brazing, a welder with an oxyacetylene torch is what you need to combine with a proper brazing rod, of course. Quite a few actually. For our story here, we had an unanticipated need to cut and weld the inlet neck to our big-block water pump housing. But whatever the welder or the process you decide to go with, preparation is still key. This can only be corrected by grinding out the pocket and repairing- welding it. Porosity is gas bubbles.plain and simple..but what is not so simple is what causes those gas bubbles. Would you prefer to share this page with others by linking to it? see more tig welding aluminum videos or go to the main TIG welding page. Lets now take a look at the two most common types of welding. With the Miller Syncrowave 210, the max amperage is set at the welder and the foot pedal operates within that range. Another difficulty you may encounter while welding aluminum is a variation in the thickness of different materials. After welding, the excess bead was carefully ground down level with a file to examine for porosity. Types of Torch Brazing How to Braze Metals with a Torch? However, the 7XX.0 aluminum-zinc casting alloys are considered fairly difficult to weld, even though they are heat-treatable. Of course, the best thing is knowing the compound of the parent metal, but since this is not always an option, doing the best job with what you got is still possible. The news here is that one welderthe Syncrowave 210can do it all. In this process, the molten aluminum is pressure-injected into a water-cooled steel mold. Some people said that all aluminum castings are weldable. The repair was done as a favorIf I were doing this repair for a customer I probably would have charged around $200, Carbide burrs designed for aluminum are best bet for grooving out cracks but grinding wheels work too ( Sometimes I use Irish Spring bar soap to prevent loading of a grinding or sanding disc), if you have AC balance, a setting of 65 or less EN helps ( since some machines have use a scale of cleaning on AC balance, a setting of around 35% cleaning works good). The 3xx.0 families (356.0, 357.0, and 319.0) are treatable by heat and can be welded with the aluminum filler alloy 4043. Our goal with this story is to let you in on a little secret: TIG welding is not only very rewarding when you get it right, it's been made a ton easier by Miller Electric with their new Syncrowave 210 machine. Are there any other options like torch mounted torch amperage controls? It usually is. This can lead to you having an irregular arc. The first and most notable way is looking at the surface. Aluminum can easily be contaminated by dirt, air, water, and even hydrogen, which can hinder a perfect welding job. When most folks think about welding, they think about MIGmetal inert gas. The 3xx.0 family are Aluminium-Silicon-Magnesium alloys except for 319.0 cast aluminum, which contains copper. | Metals that can be Dip Brazed. Easily access valuable industry resources now with full access to the digital edition of The WELDER. Can aluminum be fixed? Some of the 7xx.0 series cannot be welded. What if that welder also did stick welding, and came with an optional spool attachment to MIG weld aluminum, mild steel, and stainless steel? And with the right alloy filler, you can even join dissimilar metal types, like cast iron and steel. Enjoy full access to the digital edition of STAMPING Journal, which serves the metal stamping market with the latest technology advancements, best practices, and industry news. Amazon and the Amazon logo are trademarks of Amazon.com, Inc, or its affiliates. thats a real benefit for tig welding aluminum castings. A cleaning pass helpswhere you allow the cleaning action of the arc to etch the surface before you actually puddle the metal. He also was the author of The WELDER's "Aluminum Workshop" column from 2001 to 2020. Q: what is your favorite tig rod for cast aluminum welding? This process has a higher deposition rate than Tungsten Inert Gas welding, which affects the quality of the weld.
but a few days after I did the weld repair, I got some 4943 filler rod. Filler rod thickness ranges typically between 1/16 and 3/16 inch in diameter, and comes in 1/32-inch increments. The choice of the welder you are going to use for cast aluminum welding will greatly depend on the process you will be using MIG, TIG, or brazing. Two important factors determine the weldability of aluminum casting. You must ensure to keep the base material and aluminum rod from moisture to prevent porosity. With the cut cleaned up and the surface prepped for welding, he headed off to Miller Electric's training center in Rancho Cucamonga, California, where Miller's industrial district manager, Josh Sprinkle, guided us through the simple procedure of welding our modded pump housing. Here we have an aluminum water pump housing with its inlet facing an AN fitting that's part of the lube circuit on our Indy Maxx block. For example, aluminum can be exposed to fresh water, salt water, exhaust gas carbon, oil, and other nasty things. This baby can TIG and stick weld, and even upgrades to a spool gun for MIG welding aluminum, mild steel, and stainless steel.
When the steel casting die opens, the ejector pins extend and pop the casting out of the die. First, every piece of the aluminum cast should be treated separately, as choosing the adequate method will depend on the situation case by case. This makes melting the rod easy and filling it into the cast aluminum to patch the cast aluminum parts. Can A 2000 Watt Generator Run A Refrigerator? Besides being able to choose the correct alloy rod, you also need to pick the one with the right diameter. The ejector pins usually open and pop the casting out of the die. Most hobbyists are at the limit of their comfort zone with MIG welding, and mostly in non-critical areas at that. Clean, clean, clean! You can use mild alkali or a solvent to clean up oil, grease, or water vapor. Put the joints together by arranging them appropriately. A: Yes there are some other options. Frank Armao was an active member of the AWS D1 Committee, chairman of the AWS D1 Aluminum Secondly, aluminum castings are created using many different castings processes. But die casting is the odd one out here. Another important characteristic that must be considered is how the casting was made. We get it. It will also make choosing the filler material a nightmare. Gas flow should be regulated between 16 and 18 cubic feet per hour for aluminum up to half an inch thick. These marks are about one-eighth inches, measuring in diameter. Called MVP (multi-voltage plug), the power plugs can be swapped in seconds to work on either 115V or 230Va big advantage for the home-based DIY guy. Most Cast Aluminium can be welded. Oil soaked castings like crankcases from motorcycles, machinery parts, or even cookware, can give you fits. think brazeuse a forward and back torch motion to gently flow weld metal ahead using just enough amperage to flow the puddle. You'd expect a lot more dials, switches, and buttons on a machine that does as much as the 210, but Miller has wisely hidden them in menus opened with the small square button. The most common aluminum casting alloys are the heat-treatable 3XX.0 series, such as 356.0, 357.0, and 319.0. Usually youll find these gas pockets as you are welding, and there isnt much you can do about it besides grind out the pocket and repair-weld it. For die casting, the molten aluminum is injected with pressure into a water-cooled steel mold, making the molten aluminum solidify rapidly. These gas pockets make things very inconvenient for welders as you have to grind them out or repair weld them. What if that welder was lighter, physically more robust, and boasted a brick-and-mortar dealer network with over 500 local stores? All of these can easily and without question be welded using a 4043 as filler wire. but I know its possible because I see awesome welds posted all the time from welders who use torch mounted amperage controls. How to weld aluminum castings can be a tricky subject. You also need an oxyacetylene torch for this process as well. Its a jet pump for an outboard boat motor that hit some rocks and made some extensive cracks. A lower melting point means the filler wire will flow at lower amperageand that means it will be less likely to draw impurities out of the cast aluminum base metal. There are at least four different processes which include: Its entirely possible to weld investment castings, permanent mold castings, and sand castings. This reduces porosity further and makes the union stronger. Clean the piece that you are welding as thoroughly as possible. All we need is 1/8-inch clearance to get the radiator hose on without interfering. Aluminum requires extra care and caution during welding due to its peculiar properties, such as its susceptibility to impurities in its molten state, making it porous and weak. It has a smoother surface finishing than investment, sand, and permanent mold casting.
By using heat sinks, you can weld at a slower pace and. They are also treatable by heat treatment, and they can be welded using 5356 Aluminium filler. Best of all, inverter power supply technology is lighter in weight, and can handle more physical abuse than a transformer. However, this requires knowledge of the metals thermal and electrical conductivity. With it cooling down much slower, all of the gasses from the molten aluminum have a chance to escape out. Since too much heat can melt the aluminum and too low will not get it started, determining the right amount of it on some scrap should prepare you for the final job. Ensure heat sinks are used. Dip brazing stands out from other brazing methods, and the advantage of dip brazing is that you can braze and. To avoid defects and improve the overall appearance of the weld, use a multiple pass straight bead. Most aluminum castings can be welded, so the short answer is yes. If it is smoother than other castings, then it is definitely a die casting. We ordered an extra cast-aluminum water pump housing from Bouchillon Performance and took it over to Motech Performance where work is proceeding on our '68 Valiant project car. The 210's power supply is inverter-based, as opposed to a transformer. But if the parent metal is thicker, you are going to want a large diameter wire to avoid burn-throughs.
This technique easily evades that complication. The torch can be moved in a slight spiral or a slight zigzag in order to broaden the weld puddle and even out the heat. I used 4943 to fill in those thick areas and it wet out very well. However, when it comes to casting weldability, there are two factors to consider: Its composition and how it was manufactured. TIG welding is not only very rewarding when you get it right, it's been made a ton easier. This magazine has served the welding community in North America well for more than 20 years. That is why a post-weld heat treatment application will restore some of the properties if the accurate filler alloy is used. This process is considered clean because the alternating current acts as a cleaner, removing the oxidized layer that protects the aluminum as you weld. Easily access valuable industry resources now with full access to the digital edition of The Tube & Pipe Journal. What if you could plug it into either 230 volts or regular 115-volt household power? Dawning the right set of protective armor while welding would help keep you safe from any dangers that could accompany the job.
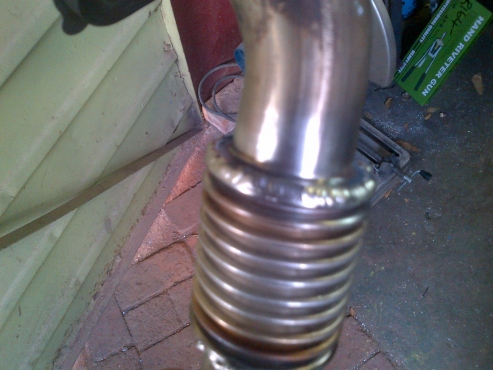
But if you still decide to do it, using a 250amp TA welder with an HTP spool gun is a good way to start. However, each of them involves proper preparation as the main factor. Super Alloy 1 comes in 1/8 and 3/32 diameter, while Super Alloy 5, the one that we need, goes between 1/16 and 3/32 diameter. Grinding with a die grinder should also be considered as part of preparation. It can be flimsy and touchy to do, but it can be done with proper preparation. Since MIG welding cast aluminum is the hardest choice, a 250amp TA welder is what we recommend, but only if you really have to. Some of the more notable ones include die casting, investment casting, permanent mold casting, or green sand casting. Tig welding aluminum is often the preferred method. TIG welding to the rescue! in diameter on the inner and outer surfaces. Some TIG welds can be done without adding fillerthese are called autogenous, and essentially fuse the two halves of the workpiece with the material that's already there. However, die castings are very different. Due to the porosity of our cast aluminum, we used the 4043 silicon alloy, which is superior at mitigating porosity and oxidation in the affected weld area. By contrast, this form of welding involves passing an electrical current through the parts that are to be joined together while applying pressure. The gas can come from lubricants, abrasive grit, moisture, hydrogen, oxides, etc. There are a few ways that welders use to weld aluminum castings. When the arc forms, the electrode melts and becomes part of the weld. Actually, some of them are considered completely unweldable. Note that the torch faces in the direction of weld movement to keep the weld enveloped by the shielding gas. Also, be sure not to weld anything until all the chemicals have evaporated. In the case of brazing, a welder with an oxyacetylene torch is what you need to combine with a proper brazing rod, of course. Quite a few actually. For our story here, we had an unanticipated need to cut and weld the inlet neck to our big-block water pump housing. But whatever the welder or the process you decide to go with, preparation is still key. This can only be corrected by grinding out the pocket and repairing- welding it. Porosity is gas bubbles.plain and simple..but what is not so simple is what causes those gas bubbles. Would you prefer to share this page with others by linking to it? see more tig welding aluminum videos or go to the main TIG welding page. Lets now take a look at the two most common types of welding. With the Miller Syncrowave 210, the max amperage is set at the welder and the foot pedal operates within that range. Another difficulty you may encounter while welding aluminum is a variation in the thickness of different materials. After welding, the excess bead was carefully ground down level with a file to examine for porosity. Types of Torch Brazing How to Braze Metals with a Torch? However, the 7XX.0 aluminum-zinc casting alloys are considered fairly difficult to weld, even though they are heat-treatable. Of course, the best thing is knowing the compound of the parent metal, but since this is not always an option, doing the best job with what you got is still possible. The news here is that one welderthe Syncrowave 210can do it all. In this process, the molten aluminum is pressure-injected into a water-cooled steel mold. Some people said that all aluminum castings are weldable. The repair was done as a favorIf I were doing this repair for a customer I probably would have charged around $200, Carbide burrs designed for aluminum are best bet for grooving out cracks but grinding wheels work too ( Sometimes I use Irish Spring bar soap to prevent loading of a grinding or sanding disc), if you have AC balance, a setting of 65 or less EN helps ( since some machines have use a scale of cleaning on AC balance, a setting of around 35% cleaning works good). The 3xx.0 families (356.0, 357.0, and 319.0) are treatable by heat and can be welded with the aluminum filler alloy 4043. Our goal with this story is to let you in on a little secret: TIG welding is not only very rewarding when you get it right, it's been made a ton easier by Miller Electric with their new Syncrowave 210 machine. Are there any other options like torch mounted torch amperage controls? It usually is. This can lead to you having an irregular arc. The first and most notable way is looking at the surface. Aluminum can easily be contaminated by dirt, air, water, and even hydrogen, which can hinder a perfect welding job. When most folks think about welding, they think about MIGmetal inert gas. The 3xx.0 family are Aluminium-Silicon-Magnesium alloys except for 319.0 cast aluminum, which contains copper. | Metals that can be Dip Brazed. Easily access valuable industry resources now with full access to the digital edition of The WELDER. Can aluminum be fixed? Some of the 7xx.0 series cannot be welded. What if that welder also did stick welding, and came with an optional spool attachment to MIG weld aluminum, mild steel, and stainless steel? And with the right alloy filler, you can even join dissimilar metal types, like cast iron and steel. Enjoy full access to the digital edition of STAMPING Journal, which serves the metal stamping market with the latest technology advancements, best practices, and industry news. Amazon and the Amazon logo are trademarks of Amazon.com, Inc, or its affiliates. thats a real benefit for tig welding aluminum castings. A cleaning pass helpswhere you allow the cleaning action of the arc to etch the surface before you actually puddle the metal. He also was the author of The WELDER's "Aluminum Workshop" column from 2001 to 2020. Q: what is your favorite tig rod for cast aluminum welding? This process has a higher deposition rate than Tungsten Inert Gas welding, which affects the quality of the weld.
but a few days after I did the weld repair, I got some 4943 filler rod. Filler rod thickness ranges typically between 1/16 and 3/16 inch in diameter, and comes in 1/32-inch increments. The choice of the welder you are going to use for cast aluminum welding will greatly depend on the process you will be using MIG, TIG, or brazing. Two important factors determine the weldability of aluminum casting. You must ensure to keep the base material and aluminum rod from moisture to prevent porosity. With the cut cleaned up and the surface prepped for welding, he headed off to Miller Electric's training center in Rancho Cucamonga, California, where Miller's industrial district manager, Josh Sprinkle, guided us through the simple procedure of welding our modded pump housing. Here we have an aluminum water pump housing with its inlet facing an AN fitting that's part of the lube circuit on our Indy Maxx block. For example, aluminum can be exposed to fresh water, salt water, exhaust gas carbon, oil, and other nasty things. This baby can TIG and stick weld, and even upgrades to a spool gun for MIG welding aluminum, mild steel, and stainless steel.
When the steel casting die opens, the ejector pins extend and pop the casting out of the die. First, every piece of the aluminum cast should be treated separately, as choosing the adequate method will depend on the situation case by case. This makes melting the rod easy and filling it into the cast aluminum to patch the cast aluminum parts. Can A 2000 Watt Generator Run A Refrigerator? Besides being able to choose the correct alloy rod, you also need to pick the one with the right diameter. The ejector pins usually open and pop the casting out of the die. Most hobbyists are at the limit of their comfort zone with MIG welding, and mostly in non-critical areas at that. Clean, clean, clean! You can use mild alkali or a solvent to clean up oil, grease, or water vapor. Put the joints together by arranging them appropriately. A: Yes there are some other options. Frank Armao was an active member of the AWS D1 Committee, chairman of the AWS D1 Aluminum Secondly, aluminum castings are created using many different castings processes. But die casting is the odd one out here. Another important characteristic that must be considered is how the casting was made. We get it. It will also make choosing the filler material a nightmare. Gas flow should be regulated between 16 and 18 cubic feet per hour for aluminum up to half an inch thick. These marks are about one-eighth inches, measuring in diameter. Called MVP (multi-voltage plug), the power plugs can be swapped in seconds to work on either 115V or 230Va big advantage for the home-based DIY guy. Most Cast Aluminium can be welded. Oil soaked castings like crankcases from motorcycles, machinery parts, or even cookware, can give you fits. think brazeuse a forward and back torch motion to gently flow weld metal ahead using just enough amperage to flow the puddle. You'd expect a lot more dials, switches, and buttons on a machine that does as much as the 210, but Miller has wisely hidden them in menus opened with the small square button. The most common aluminum casting alloys are the heat-treatable 3XX.0 series, such as 356.0, 357.0, and 319.0. Usually youll find these gas pockets as you are welding, and there isnt much you can do about it besides grind out the pocket and repair-weld it. For die casting, the molten aluminum is injected with pressure into a water-cooled steel mold, making the molten aluminum solidify rapidly. These gas pockets make things very inconvenient for welders as you have to grind them out or repair weld them. What if that welder was lighter, physically more robust, and boasted a brick-and-mortar dealer network with over 500 local stores? All of these can easily and without question be welded using a 4043 as filler wire. but I know its possible because I see awesome welds posted all the time from welders who use torch mounted amperage controls. How to weld aluminum castings can be a tricky subject. You also need an oxyacetylene torch for this process as well. Its a jet pump for an outboard boat motor that hit some rocks and made some extensive cracks. A lower melting point means the filler wire will flow at lower amperageand that means it will be less likely to draw impurities out of the cast aluminum base metal. There are at least four different processes which include: Its entirely possible to weld investment castings, permanent mold castings, and sand castings. This reduces porosity further and makes the union stronger. Clean the piece that you are welding as thoroughly as possible. All we need is 1/8-inch clearance to get the radiator hose on without interfering. Aluminum requires extra care and caution during welding due to its peculiar properties, such as its susceptibility to impurities in its molten state, making it porous and weak. It has a smoother surface finishing than investment, sand, and permanent mold casting.
By using heat sinks, you can weld at a slower pace and. They are also treatable by heat treatment, and they can be welded using 5356 Aluminium filler. Best of all, inverter power supply technology is lighter in weight, and can handle more physical abuse than a transformer. However, this requires knowledge of the metals thermal and electrical conductivity. With it cooling down much slower, all of the gasses from the molten aluminum have a chance to escape out. Since too much heat can melt the aluminum and too low will not get it started, determining the right amount of it on some scrap should prepare you for the final job. Ensure heat sinks are used. Dip brazing stands out from other brazing methods, and the advantage of dip brazing is that you can braze and. To avoid defects and improve the overall appearance of the weld, use a multiple pass straight bead. Most aluminum castings can be welded, so the short answer is yes. If it is smoother than other castings, then it is definitely a die casting. We ordered an extra cast-aluminum water pump housing from Bouchillon Performance and took it over to Motech Performance where work is proceeding on our '68 Valiant project car. The 210's power supply is inverter-based, as opposed to a transformer. But if the parent metal is thicker, you are going to want a large diameter wire to avoid burn-throughs.
This technique easily evades that complication. The torch can be moved in a slight spiral or a slight zigzag in order to broaden the weld puddle and even out the heat. I used 4943 to fill in those thick areas and it wet out very well. However, when it comes to casting weldability, there are two factors to consider: Its composition and how it was manufactured. TIG welding is not only very rewarding when you get it right, it's been made a ton easier. This magazine has served the welding community in North America well for more than 20 years. That is why a post-weld heat treatment application will restore some of the properties if the accurate filler alloy is used. This process is considered clean because the alternating current acts as a cleaner, removing the oxidized layer that protects the aluminum as you weld. Easily access valuable industry resources now with full access to the digital edition of The Tube & Pipe Journal. What if you could plug it into either 230 volts or regular 115-volt household power? Dawning the right set of protective armor while welding would help keep you safe from any dangers that could accompany the job.