xZeO>-n3lIr4}rYI4 h T'r lKr77pV~cY@u{m(z(("KKEa(A$gr/x Intense UV and infrared (IR) radiation can be generated from the arc or plasma. arc electric spray wire metco process diagram oerlikon coating thermal schematic Moreover, the presence of pores interconnected throughout the coating-thickness makes the as-sprayed coating unable to fully protect the substrate from corrosion. It is obvious that processability of different coatings to obtain high quality plays a large role in selection of an appropriate, Depends on equipment type; e.g., M2 AC-HVAF, 600700 m s. Oxide content is approximately 1.52 times the oxide content of the feedstock. Moreover, the presence of pores interconnected throughout the coating-thickness makes the as-sprayed coating unable to fully protect the substrate from corrosion. The state-of-the-art process of hardmetal coating preparation by thermal spraying is illustrated in Figure 2, showing the deposition by HVOF spraying. The residual porosity in thermal spray coatings is usually lowest in the high-velocity spray processes.
The powder of the coating material and carrier gas are fed into the exit point of the nozzle (heating zone) through an inlet to become molten. To create the plasma jet, inert plasma-forming gas, usually argon or nitrogen with minor additions of helium or hydrogen, is injected into the annular space between the two cylindrical electrodes, and a high amperage direct current (DC) arc is then struck between the electrodes. 0000020749 00000 n
The most typical energy sources in thermal spraying are thermal (and/or kinetic) energy obtained from combustion of gases, typically hydrocarbon or hydrogen, or liquids; from thermal energy obtained from electric discharges such as electric arcs or ionized plasma gases; or from purely kinetic energy sources in cold kinetic spray process. 0000012017 00000 n
0000099329 00000 n
Modification of an older version, M.F. plasma controlled spray atmosphere metco process oerlikon atmospheric coating thermal diagram schematic champro
Upon exposure to the eyes and skin, these radiations can pose a potential health hazard. In this process, a partially ionized conductive gas, known as plasma, is used to melt and propel powdered feedstock material onto the substrate. Melted particles are then forced out from the nozzle and projected toward the substrate allowing them to form a coating layer. spray combustion wire diagram oerlikon metco process thermal schematic 0000007689 00000 n
The deleterious tensile stresses in the coating can weaken the bond to the substrate and can lead to delamination [22]. Substrates that are sensitive to high temperatures may preclude the use of thermal spray and would include magnesium, composites and other low melting alloys. 0000053259 00000 n
rolling aluminum strip spray schematic approach figure ktn totalmateria 0000001351 00000 n
:PBV 0 In:*`]L-FGYcI:Tn0^\ynJtZj:|;zz Schematic diagram of a plasma spray gun. A jet of compressed air or inert gas is directed across the wire tips, atomizing the molten metal and creating a spray stream of molten droplets. principle metco 0000003317 00000 n
It is notable that in spite of the availability of several more or less differing techniques in thermal spray processes, they all have their own important niches and only minor overlaps in performance, investment and operation cost levels, and coating material processability and coating properties exist. D-guns are mainly used to deposit metals, alloys, and cermets with high density (porosity <1%) and very low oxidation. A new process called high-frequency pulse detonation using aerodynamic valves producing discrete batches of explosive gases and powders for each cycle allows spray frequencies over 60Hz (Belzunce et al., 2002). )RX61`
endstream
endobj
150 0 obj
570
endobj
151 0 obj
<< /Filter /FlateDecode /Length 150 0 R >>
stream
Among all thermal spray processes, plasma spray is the most versatile coating deposition technique widely used in the medical devices industry. (b) Top view of the surface of an as-sprayed Cr3C2-NiCr HVOF coating. Source: Tampere University of Technology. Easily oxidizing metals may require spray atmospheres in which oxygen has been eliminated, i.e., inert gas shroud or low-pressure plasma spray (LPPS) or vacuum plasma spray (VPS) processes. Bulk parts prepared by powder metallurgy are termed "hardmetals" or "cemented carbides", whereas the term "cermet" is used for TiC-Ni-based materials only. 0000002578 00000 n
0000019701 00000 n
The values and numbers may be highly material, parameter, and process/equipment sensitive and act therefore only as comparative data for general comparison of the different thermal spray processes. Pores are always present in thermal spray coatings and their geometry presents two-dimensional characteristics that are different from the pores in bulk porous materials processed by conventional processes such as powder metallurgy. A powder flame spray gun is similar, but powder suspended in a carrier gas is injected along the central axis of the gun where the wire is shown in this diagram. 0000004602 00000 n
0000009700 00000 n
By simultaneously feeding more than one material into the spray gun, highly unique composite materials can be deposited. The range of values for one specific property is significantly larger, as schematically illustrated in Figure 4. Therefore, CS materials have been improved significantly over the past few years. Regardless, coating failures can occur because the plasma and HVOF processes can generate excessive heat causing the formation of an oxide on the magnesium that is detrimental to adhesion. The arc partially ionizes the gas to form a high-temperature, electrically conductive plasma, which expands and escapes through the open end of the anode to form a very hot, high-velocity, plasma jet. 3.5. Li, in Surface Engineering of Light Alloys, 2010. In most of the thermal spray processes, this is achieved by full or partial melting of the feedstock material, while the substrate remains unmelted, i.e. Hb```f``e`c``3bd@ (l[ b1~#lJ04`, ( peV,?o``pt``4h``vM=]C/
1' x1H300A |"
endstream
endobj
175 0 obj
167
endobj
129 0 obj
<<
/Type /Page
/Parent 115 0 R
/Resources << /ColorSpace << /CS0 143 0 R /CS1 142 0 R >> /ExtGState << /GS0 164 0 R /GS1 166 0 R >>
/Font << /TT0 136 0 R /TT1 137 0 R /TT2 130 0 R /TT3 133 0 R /TT4 132 0 R
/C2_0 141 0 R /TT5 147 0 R >>
/ProcSet [ /PDF /Text ] >>
/Contents [ 145 0 R 149 0 R 151 0 R 153 0 R 155 0 R 157 0 R 159 0 R 161 0 R ]
/MediaBox [ 0 0 595 842 ]
/CropBox [ 0 0 595 842 ]
/Rotate 0
/StructParents 0
>>
endobj
130 0 obj
<<
/Type /Font
/Subtype /TrueType
/FirstChar 32
/LastChar 121
/Widths [ 278 0 0 0 0 0 0 0 0 0 0 0 0 0 0 0 0 0 0 0 0 0 0 0 0 0 0 0 0 0 0 0
0 0 0 0 0 0 0 0 722 0 0 0 0 833 0 0 0 0 0 667 0 0 0 0 0 0 0 0 0
0 0 0 0 556 0 0 0 556 0 0 0 0 0 0 278 0 0 611 611 0 389 0 333 0
0 0 0 556 ]
/Encoding /WinAnsiEncoding
/BaseFont /CPGFCH+Arial,Bold
/FontDescriptor 134 0 R
>>
endobj
131 0 obj
<<
/Type /FontDescriptor
/Ascent 935
/CapHeight 0
/Descent -211
/Flags 96
/FontBBox [ -204 -307 1000 1107 ]
/FontName /CPGFGF+ArialNarrow-BoldItalic
/ItalicAngle -15
/StemV 133
/FontFile2 170 0 R
>>
endobj
132 0 obj
<<
/Type /Font
/Subtype /TrueType
/FirstChar 32
/LastChar 150
/Widths [ 228 0 0 0 0 0 547 0 273 273 319 479 228 273 228 228 456 456 456 456
456 456 456 456 456 456 228 228 0 0 0 0 832 547 547 592 592 547
501 638 592 228 0 0 456 683 592 638 547 638 592 547 501 592 547
774 0 0 501 0 0 0 0 0 0 456 456 410 456 456 228 456 456 182 182
410 182 683 456 456 456 0 273 410 228 456 410 592 410 410 410 0
0 0 0 0 0 0 0 0 0 0 0 0 0 0 0 0 0 0 0 0 0 182 182 273 273 0 456
]
/Encoding /WinAnsiEncoding
/BaseFont /CPGFLC+ArialNarrow
/FontDescriptor 139 0 R
>>
endobj
133 0 obj
<<
/Type /Font
/Subtype /TrueType
/FirstChar 32
/LastChar 119
/Widths [ 228 0 0 0 0 0 0 0 0 0 0 0 0 0 0 0 0 0 0 0 0 0 0 0 0 0 0 0 0 0 0 0
0 592 0 0 0 0 0 0 0 0 0 0 0 0 0 0 0 0 0 0 0 0 0 0 0 0 0 0 0 0 0
0 0 456 0 456 501 456 0 501 0 228 0 0 0 0 501 501 501 0 319 456
273 0 0 638 ]
/Encoding /WinAnsiEncoding
/BaseFont /CPGFGF+ArialNarrow-BoldItalic
/FontDescriptor 131 0 R
>>
endobj
134 0 obj
<<
/Type /FontDescriptor
/Ascent 905
/CapHeight 0
/Descent -211
/Flags 32
/FontBBox [ -628 -376 2034 1048 ]
/FontName /CPGFCH+Arial,Bold
/ItalicAngle 0
/StemV 133
/FontFile2 171 0 R
>>
endobj
135 0 obj
<<
/Type /FontDescriptor
/Ascent 905
/CapHeight 0
/Descent -211
/Flags 32
/FontBBox [ -665 -325 2028 1037 ]
/FontName /CPGCDP+Arial
/ItalicAngle 0
/StemV 0
/FontFile2 165 0 R
>>
endobj
136 0 obj
<<
/Type /Font
/Subtype /TrueType
/FirstChar 32
/LastChar 121
/Widths [ 278 0 0 0 0 0 0 0 0 0 0 0 0 333 278 278 0 556 556 0 0 0 0 556 0 556
278 0 0 0 0 0 0 0 0 0 0 0 0 0 722 0 0 0 0 833 0 778 667 0 0 667
0 0 667 944 0 0 0 0 0 0 0 556 0 556 556 500 0 556 278 556 0 222
0 0 222 833 0 556 556 0 333 500 278 556 0 722 0 500 ]
/Encoding /WinAnsiEncoding
/BaseFont /CPGCDP+Arial
/FontDescriptor 135 0 R
>>
endobj
137 0 obj
<<
/Type /Font
/Subtype /TrueType
/FirstChar 32
/LastChar 118
/Widths [ 250 0 0 0 0 0 0 0 0 0 0 0 0 0 0 0 0 0 0 0 0 0 0 0 0 0 0 0 0 0 0 0
0 0 0 0 0 0 0 0 0 0 0 0 0 0 0 833 0 0 0 611 0 0 0 0 0 0 0 0 0 0
0 0 0 0 0 444 0 500 0 0 0 333 0 0 0 0 0 0 0 0 389 444 0 611 556
]
/Encoding /WinAnsiEncoding
/BaseFont /CPGEOA+BookAntiqua-Bold
/FontDescriptor 138 0 R
>>
endobj
138 0 obj
<<
/Type /FontDescriptor
/Ascent 923
/CapHeight 0
/Descent -282
/Flags 34
/FontBBox [ -134 -337 1193 1021 ]
/FontName /CPGEOA+BookAntiqua-Bold
/ItalicAngle 0
/StemV 133
/FontFile2 162 0 R
>>
endobj
139 0 obj
<<
/Type /FontDescriptor
/Ascent 935
/CapHeight 718
/Descent -211
/Flags 32
/FontBBox [ -182 -307 1000 1086 ]
/FontName /CPGFLC+ArialNarrow
/ItalicAngle 0
/StemV 78
/XHeight 515
/FontFile2 168 0 R
>>
endobj
140 0 obj
<< /Filter /FlateDecode /Length 220 >>
stream
Schematic diagram of a high-velocity oxy-fuel (HVOF) spray gun. 0000006437 00000 n
Also, the traditional terminology for these composites in these areas is different and leads often to misunderstandings (Berger, 2007). corporations pts resodyn schematic ?XN+q{/]0'q9}1,XwI-` k The other main hazards from the plasma process are electrical safety and UV radiation. Thermal spray is a technology that allows the development of large parts, which cannot be produced by powder metallurgy for technical and economical reasons, with hardmetal characteristics via the application of hardmetal coatings (Berger, 2007). APS system (left) and plasma gun in operation (right). schematic thermal spray modification enhancing resistance erosion techniques components surface engineering processes categorized velocity arc As the tips melt, additional wire is fed into the arc, making this a continuous process, with the two wires serving both as feedstock material and as consumable electrodes. 0000001918 00000 n
0000022363 00000 n
0000010988 00000 n
spraying coatings photocatalytic Therefore, general features of the thermal spray process, physical phenomena of the interaction of spray particles with the spraying flame and droplet impact, coating microstructure features, microstructure/property relations, and coating/substrate adhesion are introduced in this chapter, based on state-of-the-art thermal spray coating developments that effectively achieve successful surface modification of light metals. (b) SEM of the feedstock powder. For those interested in more detailed information on traditional thermal spray processes, additional information can be found in the Handbook of Thermal Spray Technology, published by the Thermal Spray Society of ASM International (Davis, 2004), or in Chapter 11 Thermal Spraying and Cold Spraying in volume 3, part 1, of the 9th edition of the Welding Handbook, published by the American Welding Society (Smith et al., 2007). Therefore, general features of the, Berger, Hermel, Vuoristo, Mntyl, Lengauer, & Ettmayer, 1996, m. Schematic of the detonation gun (Kadyrov and Kadyrov, 1995). In addition, interfacial instability due to differing viscosities, along with the resulting interfacial roll-ups and vortices, promotes interfacial bonding by increasing the interfacial area, giving rise to material mixing at the interface and providing mechanical interlocking between the two materials [21]. 6 0 obj 59 0 obj
<<
/Linearized 1
/O 61
/H [ 1421 497 ]
/L 778043
/E 111643
/N 12
/T 776745
>>
endobj
xref
59 49
0000000016 00000 n
Flame flame spraying, wire and powder method; electric arc electric arc wire spraying; detonation detonation gun spraying; HVOF high-velocity oxygen-fuel spraying; HVAF high-velocity air-fuel spraying; LPPS/VPS low-pressure/vacuum plasma spraying; LPCS low-pressure cold spraying; HPCS high-pressure cold spraying/kinetic spraying; APS atmospheric plasma spraying. 0000006164 00000 n
A recent article of Astakhov (2008) presents the developments of the process. Major commercial thermal spray process technologies can be broadly grouped into two basic categories: those that use electrical energy and those that use chemical energy. The process chamber is initially sealed and pumped down as far as possible with the spray gun off; it is then back-filled to the desired operating pressure with an inert gas, such as argon, before coating deposition begins. 0000046881 00000 n
In Fig. The segmentation cracks are formed during the deposition process mainly by applying high substrate temperatures above 500C in combination with high particle temperatures [3537]. ), type of oxidizer in combustion, etc. Thus, preparation of thermal spray coatings can also be considered as the preparation of a shaped hardmetal using a two-step technology: first, feedstock powder preparation and second, the spray process.
HTPn0+|\C IKJN&E*Nd_g?gC}t:Kqtk /XnzPd$7psPB~xlR}fR The peening effect of these high-velocity particles impacting the work-piece surface can produce coatings with very little porosity (near theoretical density) and also create a more favorable residual stress state in the spray-deposited material. Cold spray technology is the logical choice for dimensional restoration of a variety of engineering materials and for applications where the high temperatures associated with conventional thermal spray technology can result in undesirable metallurgical transformations, including grain growth, as well as oxidation, that can have detrimental effects on bond strength and porosity and/or damage the underlying substrate. For coating formation, plastic deformation of the feedstock particles at the moment of impact is a precondition after acceleration inside or outside of the spray gun. Hardmetals are one of the most important group of materials processed by thermal spray processes into coatings. gas in the chamber is continuously pumped out to balance the inflow of plasma-forming gas and powder feed carrier gas, with an operating pressure in the chamber typically above 6 MPa (60 bar or 45 torr). 0000010876 00000 n
This method belongs to the group of thermal spray processes defined in ISO 14917:2017 and described in detail in Ref. Although typically the same hard phase-binder metal composite materials are used, the technical development in powder metallurgy and thermal spray were practically independent of each other. 0000008370 00000 n
Po*o](b/h^, P(kD0!D@YYKy!D &DPn^Z;#Gc(N
BT{_c'YWpQL2{\nu?^
RPN}~FvZ>[KtoR19jOc2MN^1&0MXdYyet@x*g
Good corrosion protection is also achieved by dense, impermeable, cold sprayed coatings.
Illustration of hardmetal coating preparation by the high-velocity oxy-fuel (HVOF) spray process. 0000006320 00000 n
Additionally, during solidification of the sprayed aluminium particles, tensile stresses form in the coating while the underlying substrate material contains compressive stresses. Thermal spray processes have been widely used in various industrial fields to enhance surface properties of various engineering parts. Here a liquid-fueled process is shown. As the combustion gas is accelerated to supersonic velocities, the jet expands and cools as thermal energy is converted to kinetic energy.
% WC-12Co, WC-17Co, WC-10Co-4Cr, WC-20"CrC"-7Ni and Cr3C2-(20-25)NiCr (all compositions are in weight percent unless otherwise indicated) are the main commercially available compositions. Figure 1. (c) Dense WC-Co coating. A more specialized book deals with coating preparation by high-velocity oxy-fuel (HVOF) spraying (Sobolev, Guilemany, & Nutting, 2004). Depending on the type of energy source, thermal spray processes can be further classified according to the spray gun principle or design, type of feedstock material used in the process, type of fuel (gas or liquid), type of deposition atmosphere (atmospheric, low/high pressure, inert gas, under water, etc. fG4o$^ZY#[!ckej` G9CM&M*p-f%uj-LS This can become a particular concern in an application that requires a relatively thick deposit because these stresses often cause delamination and often limit the maximum deposit thickness that can be achieved. The ability to deposit materials at high rates and produce thick deposits makes it suitable for dimensional restoration of aluminium, magnesium, steel, nickel, copper and other common engineering materials. 3.3) the tips of two metal wires are brought together at a slight angle and an electric arc is struck between them, melting the material at the wire tips. Schematic diagram of a twin-wire arc spray gun. 0000088453 00000 n
YUiN/B_JP_r8|DV:! depends on porosity of the coating on steel, Current status and future directions of thermal spray coatings and techniques, Future Development of Thermal Spray Coatings, Davis, 2004; Tucker, 2013; Fauchais et al., 2014, Environmentally Oriented Modernization of Power Boilers, High-Temperature Behaviour of Thermal Barrier and Bond Coatings in Oxidizing and Corrosive Atmospheres, Materials Surface Processing by Directed Energy Techniques, Introduction to Supersonic Particle Deposition, Resistance to atmospheric and heat corrosion, Electrically conductive and solderable coatings, High velocity oxy-fuel thermal spray (HVOF), Repair operations Abrasion or erosion resistance, Resistance to fretting, galling or adhesive wear. apparatus coatings amorphous sprayed research reprinted This problem is compounded when the substrate material is different from the coating material in terms of hardness and density and there is a significant variation in the coefficient of thermal expansion. alloys 0000007038 00000 n
Figure 2. A typical flame spray device (Fig. Powder particles entrained in this high-velocity gas jet are accelerated up to velocities of the order of 4501000 m/s (14753280 ft/s), depending upon the spray device, spray material, and operating conditions. spraying coating zinc Electrical processes typically use either an electric arc or an electrically driven plasma to heat and melt the spray material.


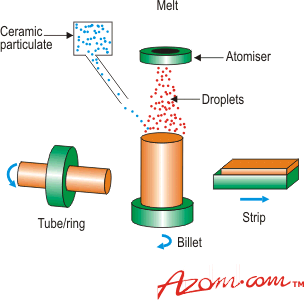




