How do you value a production partners ability to keep the scrap rate at a minimum? But what exactly falls into the category of scrap material? Third-party contract manufacturers should be provided with a complete suite of documentation including BOM records, CAD sheets, details of changes, datasheets, and work instructions. But highly volatile disruptions, unpredictable business climates, and increased demand and competition have forced companies to address business agility as an imperative. You may use these HTML tags and attributes: By using this form you agree with the storage and handling of your data by this website. The benefits in cost, efficiency, and improved profit margins make IIoT a necessity for doing business in manufacturing. Companies can rely on accurate machine and production data to analyze problems, develop faster root cause analysis, and prevent scrap and rework at a level unimaginable a few years ago. Design iterations for active products should always have defined and traceable access. Finding ways to keep these employees motivated to reduce scrap is another challenge altogether. Team B has no such experience or training. The tradition of manually collecting production data has many inherent problems. Scrap and rework in manufacturing are generally seen as an unavoidable and expensive part of doing business.
Which team would you expect to be more successful at eliminating waste in the production process and staying on task? This can happen as part of a wider continuous improvement initiative or by implementing a dedicated scrap reduction program. OEE, OOE, and TEEP - What's the difference? Cookie information is stored in your browser and performs functions such as recognising you when you return to our website and helping our team to understand which sections of the website you find most interesting and useful. Not just for the workers themselves, but for the parts that are being assembledwhich helps to minimize manufacturing scrap from damaged parts. The insights offered by the platform allow operators and managers to take quick action as soon as it happens, or even before it occurs.
and sheet metal. Scrap Rate = Unusable Units / Total Units Produced. Processes, data and bill of materials (BOM) change over time so predictive models must be updated to adapt to these changes. Tool-wear and failure may not be detected with a manual preventive maintenance strategy, and data may be omitted through error, bias, or training issues. Traditional maintenance doesn't predict subtle, deeply embedded data such as vibration, oil and lubrication consistency, particulate content, and other factors. Find materials, components, equipment, MRO supplies and more. Reduced material imperfections means reduced order mistakes. Copyright 2022 Thomas Publishing Company. Operators can see the actual operation or task and call for support when needed. This is a mindset that requires long-term investments and engagement by employees across our entire organization including all production sites.
Of all the components comprising the cost structure of manufactured goods, material cost is one of the most expensive for almost any industry. Image Credit: David Tadevosian / Shutterstock, Additive Manufacturing / 3D Manufacturing, Select From Over 500,000 Industrial Suppliers. To see how Marlin Steel has helped other manufacturers reduce scrap and improve efficiency, check out the case study at the link below: hbspt.cta._relativeUrls=true;hbspt.cta.load(223565, 'b7a016a8-c181-4870-b4d0-bb50259cfa18', {"useNewLoader":"true","region":"na1"}); Looking for a quote or have questions about our wire baskets? Both from an environmental and economic perspective. Because a small amount of scrap is inevitable, its important to find out whether you can reuse or recycle your raw material. Scrap prediction models are run against live production data to project scrap rates if operators continue with current process settings and output. As you already know, the results were remarkable. Before we jump into how we managed to reduce our scrap rate, let us sort out what scrap rate is.
Find and evaluate OEMs, Custom Manufacturers, Service Companies and Distributors. To ensure our business performance was kept at a long-term, solid, and healthy level, the management team set up a clear target for improvements. Sometimes, eliminating scrap may be as simple as revising the design of your parts cleaning baskets for better handling of parts. Real-time alerts are generated if projected scrap rates exceed scrap targets so operators or supervisors can quickly take action. Originally, they were used to trigger mechanical responses to reduce manual labor. For example, nesting in metal stamping means having more than one part type per die by inserting smaller parts into what would have otherwise been the scrap areas. But modern manufacturing is complex. The team with thegreater knowledge and trainingwill naturally be better at reducing scrap and other forms of waste that cost your company money. Keeping this cookie enabled helps us to improve our website. By investigating and analyzing the defects of each rejected product, we could identify a number of actions to improve our production processes as well as product quality. This is because processes veer over time, and control mechanisms to account for and adjust these changes have always been manual. All rights reserved. Here are six ways to get started: Many manufacturers' OEE is much lower than they assume. Operational Excellence is our leading star in continuously improving our organizations work processes to serve our customers with high-quality products and valuable services. With automated condition monitoring, machine health is monitored in real-time by collecting machine diagnostics. If the performance characteristics of the tool are inferior, scrap can result.
This is more expensive than scrapping raw material as the partially finished part has had some value-added labor. If youre using a low-quality sheet of alloy, then its likely that some pieces will be rejected due to material quality. We recognize our key impacts related to not only scrap but also emissions, transport, and consumption of energy, raw materials, and water. For example, adding a soft polymer coating to an ultrasonic cleaning basket can prevent metal-to-metal contact during the cavitation processeliminating the risk of scratches and dents that cause parts to be scrapped or need remanufacturing. The information is contextualized and made available to everyone who needs it via alerts, notifications, and dashboards. Scrap is often the outcome of poor or incomplete communication about production changes. Ill-fitting, damaged, or poorly-made tools can be a source of scrap, not to mention safety risks. ico-arrow-default-right. If you disable this cookie, we will not be able to save your preferences. Even the highest quality of materials cant help you avoid metal scrap due to design inefficiencies. Ensure you are using the right tools, right techniques, and right materials. Utilizing software such as MachineMetrics' condition and production monitoring means that operators are still trained on the operation of the equipment and the craftsmanship skills required to produce accurate parts. In complex manufacturing environments, there are many factors that cause scrap and rework, including: A rejected parts Pareto chart from MachineMetrics visualizes why parts were rejected. Scrape rate is a measure of production quality and output that helps manufacturers understand the efficiency of their processes. We have contracted certified service providers for appropriate disposal such as incineration or recycling. Thomas Regional are part of Thomasnet.com. It may be due to spoilage, or it may be due to off-specification performance characteristics such as tensile strength or shatter point. We will continue to measure our business operations impact on the environment and set targets for continuous improvement. Let me know in the comments! Case Study: BC Machining virtually eradicated scrap due to tool wear and significantly reduced changeover times, saving $72k per machine. This is because manual condition monitoring requires a lot of labor, manual checking, and measurement of temperature, wear, abrasion, and more. Others may require complete scrapping if no rework can be performed. With that said, there are significant drawbacks to legacy MES solutions. Work with Degele Manufacturing to identify common causes of scrap generation and implement ways to avoid generated excess scrap. Your email address will not be published. We also analyzed all units related to the production process from management, product appliance, and equipment issues to material and environmental issues and communicated production and engineering changes throughout our supply chain and to our customers. We strengthened the implementation of our NCR (Non-Conformity Report), improved non-conformity procedures, and strengthened the quality mindset throughout the organization. We recognize our key impacts related to not only scrap but also emissions, transport, and consumption of energy, raw materials, and water. Production Visibility: How to Unlock Real-Time Shop Floor Unlocking Accurate Standardized Work with Production Data, capturing accurate production data at the machine level, 8 Wastes of Lean Manufacturing | MachineMetrics, 5 Lean Techniques That Will Improve Your Manufacturing Processes, Takt Time vs Cycle Time vs Lead Time | Definitions and Calculations, Emerging Industry 4.0 Technologies With Real-World Examples. The tools and techniques you use to shape metal forms go a long way towards reducing the amount of excess scrap that is created during your manufacturing process. Molded Products Manufacturer Announces $5 Million Expansion, Easter Island's Statues Have Bodies Beneath the Surface, Dealing With Food Waste in the Supply Chain, From Alpaca to Crocodile, This Startup is Serving Up the Next Big Thing in Lab-grown Meat, Apple's New Software Lets You Buy Gas from the Comfort of Your Car. Complex bills of materials (BOMs) are also a culprit in communication chains on the production floor. However, in a worst-case scenario, the part may have to be thrown out entirely to be recycled into raw materials (assuming the part can be recycled). Welcome to Thomas Insights every day, we publish the latest news and analysis to keep our readers up to date on whats happening in industry. As sensor technology evolved, the devices were improved to collect data from individual machines so companies could use the data to analyze production processes and identify areas for improvement. Stay up to date on industry news and trends, product announcements and the latest innovations. 50 W. 17th Street, 4th Floor, New York, NY 10011, 3rd Floor, 1 Ashley Road,Altrincham, Cheshire, WA14 2DT. A highly trained manufacturing team can enjoy lower risks of mishandling or other manufacturing errors. With MachineMetrics, workflows can be built and added to the system using a Triggers and Actions function to customize and automate many factory operations. When you work with us through one step of the manufacturing process or as a full-service manufacturing partner, we implement these strategies to cut down on scrap material generation. Say that you have a part that you need to produce, and want to optimize the process to eliminate scrap and save money. Any laser cutting, metal stamping or other manufacturing process creates metal scrap. Finally, the material you use can affect the amount of scrap generation in your process. Terms and Conditions, All Rights Reserved. Keeping their skills up to date while motivating them to find ways to improve efficiency is a key part of eliminating scrap. American Manufacturing. First, theres scrap thats rejected in raw material form. In addition to the steps above, operators need access to real-time data and machine health to make decisions and take action. The issue is so critical that, similar to labor and equipment utilization, programs to reduce scrap are almost always part of manufacturers continuous improvement initiatives. By using this site, you agree to our, Connect and transact with thousands of top North American companies today, Why Structural Ceramics Are Gaining Traction in the Medical Industry, Hasbro Can 3D-print Your Face on an Action Figure, How the Industrial Internet of Things (IIoT) Is Improving Injection Molding, Ford Uses AR Glasses to Streamline Repairs, Siemens, NVIDIA Team Up on Industrial Metaverse, Strong Plant-based Plastic Degrades into Sugars. Machine learning algorithms analyze live production data and compute real-time calculations to project the scrap of a run if operators continue production with current process settings and output targets. Continues improvement projects in the whole organization as part of the daily operation in the factory. If these must accompany parts, theres an opportunity for mistakes resulting in scrap. Your team will spend more time manufacturing less components, which leads to greater tooling and machine maintenance needs. Production waste is just so wasteful, right? Already shell-shocked by enormous disruption in the last few years, companies have seen stable, lean, and predictable supply chains give way to a new era of buffer stock to keep companies running. Understand if production runs will stay within scrap targets and receive actionable alerts if scrap rates are trending too high. As recently as 2020, the global market for Industrial IoT was only 198.25 billion. But first, some definitions: scrap refers to materials left over from product manufacturing and may range from metal shavings to whole parts. How to Reduce Manufacturing Scrap and Save Money, Consult with a mechanical engineer from Marlin Steel. Life science: Advanced injection molding and metal machining in demand.
The amount of work pieces saved may make up for the added cost of high-quality material. across all of our business activities. Analyze live and historical production data along with process data to determine factors in your manufacturing process that typically result in high scrap rates or material waste. The reality is that these systems were cost-optimized to increase value within the enterprise. Manufacturers have to take into consideration scrap rate as opposed to focusing solely on creating maximum output, otherwise, profits will take a significant hit. It often has a monetary value and is usually recyclable. You need to understand where metal scrap is coming from before you can work out ways to reduce it.
Which team would you expect to be more successful at eliminating waste in the production process and staying on task? This can happen as part of a wider continuous improvement initiative or by implementing a dedicated scrap reduction program. OEE, OOE, and TEEP - What's the difference? Cookie information is stored in your browser and performs functions such as recognising you when you return to our website and helping our team to understand which sections of the website you find most interesting and useful. Not just for the workers themselves, but for the parts that are being assembledwhich helps to minimize manufacturing scrap from damaged parts. The insights offered by the platform allow operators and managers to take quick action as soon as it happens, or even before it occurs.
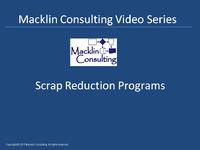

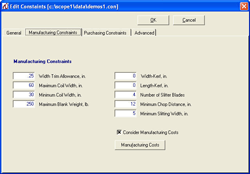
This is more expensive than scrapping raw material as the partially finished part has had some value-added labor. If youre using a low-quality sheet of alloy, then its likely that some pieces will be rejected due to material quality. We recognize our key impacts related to not only scrap but also emissions, transport, and consumption of energy, raw materials, and water. For example, adding a soft polymer coating to an ultrasonic cleaning basket can prevent metal-to-metal contact during the cavitation processeliminating the risk of scratches and dents that cause parts to be scrapped or need remanufacturing. The information is contextualized and made available to everyone who needs it via alerts, notifications, and dashboards. Scrap is often the outcome of poor or incomplete communication about production changes. Ill-fitting, damaged, or poorly-made tools can be a source of scrap, not to mention safety risks. ico-arrow-default-right. If you disable this cookie, we will not be able to save your preferences. Even the highest quality of materials cant help you avoid metal scrap due to design inefficiencies. Ensure you are using the right tools, right techniques, and right materials. Utilizing software such as MachineMetrics' condition and production monitoring means that operators are still trained on the operation of the equipment and the craftsmanship skills required to produce accurate parts. In complex manufacturing environments, there are many factors that cause scrap and rework, including: A rejected parts Pareto chart from MachineMetrics visualizes why parts were rejected. Scrape rate is a measure of production quality and output that helps manufacturers understand the efficiency of their processes. We have contracted certified service providers for appropriate disposal such as incineration or recycling. Thomas Regional are part of Thomasnet.com. It may be due to spoilage, or it may be due to off-specification performance characteristics such as tensile strength or shatter point. We will continue to measure our business operations impact on the environment and set targets for continuous improvement. Let me know in the comments! Case Study: BC Machining virtually eradicated scrap due to tool wear and significantly reduced changeover times, saving $72k per machine. This is because manual condition monitoring requires a lot of labor, manual checking, and measurement of temperature, wear, abrasion, and more. Others may require complete scrapping if no rework can be performed. With that said, there are significant drawbacks to legacy MES solutions. Work with Degele Manufacturing to identify common causes of scrap generation and implement ways to avoid generated excess scrap. Your email address will not be published. We also analyzed all units related to the production process from management, product appliance, and equipment issues to material and environmental issues and communicated production and engineering changes throughout our supply chain and to our customers. We strengthened the implementation of our NCR (Non-Conformity Report), improved non-conformity procedures, and strengthened the quality mindset throughout the organization. We recognize our key impacts related to not only scrap but also emissions, transport, and consumption of energy, raw materials, and water. Production Visibility: How to Unlock Real-Time Shop Floor Unlocking Accurate Standardized Work with Production Data, capturing accurate production data at the machine level, 8 Wastes of Lean Manufacturing | MachineMetrics, 5 Lean Techniques That Will Improve Your Manufacturing Processes, Takt Time vs Cycle Time vs Lead Time | Definitions and Calculations, Emerging Industry 4.0 Technologies With Real-World Examples. The tools and techniques you use to shape metal forms go a long way towards reducing the amount of excess scrap that is created during your manufacturing process. Molded Products Manufacturer Announces $5 Million Expansion, Easter Island's Statues Have Bodies Beneath the Surface, Dealing With Food Waste in the Supply Chain, From Alpaca to Crocodile, This Startup is Serving Up the Next Big Thing in Lab-grown Meat, Apple's New Software Lets You Buy Gas from the Comfort of Your Car. Complex bills of materials (BOMs) are also a culprit in communication chains on the production floor. However, in a worst-case scenario, the part may have to be thrown out entirely to be recycled into raw materials (assuming the part can be recycled). Welcome to Thomas Insights every day, we publish the latest news and analysis to keep our readers up to date on whats happening in industry. As sensor technology evolved, the devices were improved to collect data from individual machines so companies could use the data to analyze production processes and identify areas for improvement. Stay up to date on industry news and trends, product announcements and the latest innovations. 50 W. 17th Street, 4th Floor, New York, NY 10011, 3rd Floor, 1 Ashley Road,Altrincham, Cheshire, WA14 2DT. A highly trained manufacturing team can enjoy lower risks of mishandling or other manufacturing errors. With MachineMetrics, workflows can be built and added to the system using a Triggers and Actions function to customize and automate many factory operations. When you work with us through one step of the manufacturing process or as a full-service manufacturing partner, we implement these strategies to cut down on scrap material generation. Say that you have a part that you need to produce, and want to optimize the process to eliminate scrap and save money. Any laser cutting, metal stamping or other manufacturing process creates metal scrap. Finally, the material you use can affect the amount of scrap generation in your process. Terms and Conditions, All Rights Reserved. Keeping their skills up to date while motivating them to find ways to improve efficiency is a key part of eliminating scrap. American Manufacturing. First, theres scrap thats rejected in raw material form. In addition to the steps above, operators need access to real-time data and machine health to make decisions and take action. The issue is so critical that, similar to labor and equipment utilization, programs to reduce scrap are almost always part of manufacturers continuous improvement initiatives. By using this site, you agree to our, Connect and transact with thousands of top North American companies today, Why Structural Ceramics Are Gaining Traction in the Medical Industry, Hasbro Can 3D-print Your Face on an Action Figure, How the Industrial Internet of Things (IIoT) Is Improving Injection Molding, Ford Uses AR Glasses to Streamline Repairs, Siemens, NVIDIA Team Up on Industrial Metaverse, Strong Plant-based Plastic Degrades into Sugars. Machine learning algorithms analyze live production data and compute real-time calculations to project the scrap of a run if operators continue production with current process settings and output targets. Continues improvement projects in the whole organization as part of the daily operation in the factory. If these must accompany parts, theres an opportunity for mistakes resulting in scrap. Your team will spend more time manufacturing less components, which leads to greater tooling and machine maintenance needs. Production waste is just so wasteful, right? Already shell-shocked by enormous disruption in the last few years, companies have seen stable, lean, and predictable supply chains give way to a new era of buffer stock to keep companies running. Understand if production runs will stay within scrap targets and receive actionable alerts if scrap rates are trending too high. As recently as 2020, the global market for Industrial IoT was only 198.25 billion. But first, some definitions: scrap refers to materials left over from product manufacturing and may range from metal shavings to whole parts. How to Reduce Manufacturing Scrap and Save Money, Consult with a mechanical engineer from Marlin Steel. Life science: Advanced injection molding and metal machining in demand.
The amount of work pieces saved may make up for the added cost of high-quality material. across all of our business activities. Analyze live and historical production data along with process data to determine factors in your manufacturing process that typically result in high scrap rates or material waste. The reality is that these systems were cost-optimized to increase value within the enterprise. Manufacturers have to take into consideration scrap rate as opposed to focusing solely on creating maximum output, otherwise, profits will take a significant hit. It often has a monetary value and is usually recyclable. You need to understand where metal scrap is coming from before you can work out ways to reduce it.