However, dimensions and other elements of the plan may vary between the metric and standard versions. Keep these screws clear of the table saw's miter slot locations.
Or in extreme cases, move just enough to cause a kickback. I love a sled, both crosscut, and miter. It's 1 pass through the table saw, as opposed to 6 - 8 passes at the jointer, for a glue quality edge. Save my name, email, and website in this browser for the next time I comment. I gave up. They are time tested in his own commercial cabinet shop. Attach the braces to the back panel so the bottom ends of the three parts a re-flush. Very difficult to get it square to the fence in the manner. Your email address will not be published. Drill the 1/4"-diameter pilot holes 3-12" deep and as straight as you can. If for any reason you are not satisfied with the merchandise you ordered, just return it within 90 days to receive a refund in the manner of original payment for merchandise only. The problem with both is that tippy start. I managed to "Save As" and capture the image. It uses inches and feet for measurement. Pull out your contact cement, J-roller and spacers so you can cover the top and bottom of the core with plastic laminate (pieces 3 and 4). Assemble the leg by gluing and screwing the two side braces (pieces 12) to the back (piece 11). I saw an idea like this on Izzy Swans YouTube channel.
However, having large infeed and outfeed tables for every machine takes up a considerable amount of space that can, in many cases, be better utilized. Creating 3/4"-wide dadoes across the filler strip in order to accommodate the folding outfeed table's leg pivot brackets. Once the sheet is on the table, well actually, partially on the table is more accurate, since the end of the sheet is probably on the floor, you walk to the back of the sheet, lift it up, and then try to walk forward, feeding the sheet into the blade, while trying to keep it tight to the fence. If the extension table will be used in only one position, such as right behind the blade, the rail could be made exactly as wide as the table. The unit I came up with met the criteria I had outlined and really did make cutting the rest of the sheets very easy. Glue and screw the pivot brackets into their dadoes, then attach the filler strip to the core with more glue and screws. To make the adjustable leg, I measured the table heights of various machines I might use the table with and identified the tallest and lowest tables. Get this project rolling by cutting the MDF table core top and bottom (pieces 1 and 2) to size and gluing them together. I would advise against having a rail protrude from the edge of the machines table as it would likely be in the way and catch on things. We also realized not only it would cut our time by 60 percent ripping plywood, it was even faster for jointing lumber since instead of several passes through the jointer, it was one pass through the table saw, using a rip sled. An option to this is to use a roller stand. Not quite sure how to make that solid, but I think with an aluminum front rail on the saw, I don't think its a good idea to clamp directly to the metal. Latest Forum Topics. Thats where this station comes in. Shop drawings are not available for every plan. LJ will not be held liable for the actions of any user. Looking for information on designing your projects? At 2 from each end of the inside post, and on opposite faces, drill and counterbore for a T-nut. Well, after getting a provisional patent, we did start selling them. After having used it for a few years, we were talked into making them available by the owner of a couple Woodcraft Stores. -- "The only limits to our realization of tomorrow will be our doubts of today." Like this one by Izzy Swan: I saw your reference to Izzys design in the video. A forum community dedicated to router and woodworking professionals and enthusiasts. After trying a number of ideas, I settled on a 1-1/8 9/16 rectangular mounting rail made from a piece of hardwood. The rail must be mounted to the machine securely at a height that allows the extension table to sit at exactly the height of the machine table. For the best experience on our site, be sure to turn on Javascript in your browser. For international returns, please click here. If using the table with multiple machines, alignment marks or stops on an adjustable leg could reduce setup time. and see the demo video found at the bottom of the page. The top of the clip-on support is even with the top of the saw. Machine the outside posts to 1-1/2 3/4 and inside post to 3/4 1/2, cut them to the same length (which you have to determine based on the heights of your machines), and mill 7/32 deep grooves down the centers of the two outside posts so the inner post slides freely. Maker of the world's finest Infeed and Outfeed Systems for Table Saws. Mounting the leg onto the folding outfeed table with the help of some 1/2" spacers. In addition, a machine with larger tables is heavier, harder to move, occupies more space and usually costs more. It is finished! Since the braces must pivot on the top ends, first round them over on your band saw, and step to the drill press to bore centered bolt holes. The problem with both is that tippy start. This simple easy to make jig can take away the tippy part. Click Here to Download the Drawings and Materials List. Discover more about the small businesses partnering with Amazon and Amazons commitment to empowering them. -- Visit the forest and appreciate the source of our crafts raw material. It should fold, so storing it would be simple. What really didnt help was the fact I have a problem with sciatica. Next come the guide strips (pieces 13). Unless I wanted to spend a large amount of money on a sliding table saw, which I had no room for anyway, I was out of luck. Attach a Rail Wong machines and attaches a solid wood rail to the rear edge of his band saw table. Izzy didnt offer one that fit my Grizzly saw so I was going to have to make my own no matter what. I wrapped hardwood edging all around the table. Mark and trim the bottom corners of the leg extension so it nests completely against the leg stop. The end of the bearing spacer was quite thin, so to increase the bearing surface, I added a washer. Do it yourself, do it better, do it with WORX. Also, its easiest to drill a small hole first to set the location of the hole, then use a larger bit to enlarge the hole. Milling a pair of miter slots into the outfeed table for the table saw stand with the router to finish the woodworking project. Different wood requires different woodworking strategies - from cutting to finishing. However, having a wider rail allows greater flexibility in positioning the table for optimum support. A shop-made extension table can be made of sufficient accuracy for either application if care is taken choosing appropriate materials and in construction. There are pros and cons to each approach. Fit a strip of back edging (piece 9) to the side edging, and install it. I love a sled, both crosscut, and miter. | Do Not Sell My Data
I started considering the entire process, from lifting the sheet onto the saw, to the act of walking forward, while holding up the sheet and trying to hold it tight to the rip fence. I positioned the leg stop assembly so the bottom face of piece 24 is 12-5/8" up from the floor. This is the one you probably want if you are outside the United States. It tries to feed the sheet on an angle, again creating the perfect condition for a kickback. Locked and Loaded With the support fence in place and the shop-made clamping device engaged, Wong can be sure his support table will stay in place while working. Very expensive, and also very heavy. Make the table pivot brackets about a quarter inch longer than necessary, and set them aside. That said, I am considering making one myself. Constructing the leg for the fold down outfeed table saw stand table. However, this does not impact our recommendations.). PO Box 808 It also needed to be able to go on or off the saw quickly, so it was not in the way, when not needed. Mounting the folding outfeed table to the table saw stand. I hope to be able to use my Incra Miter Gauge to cut some pieces for an upcoming project that will require 20 inch cross cuts. Install the T-nut, then assemble the leg with 1/4-20 jig knobs and washers. You may have noticed I was talking about the short blade to edge issue with some saws. Make the pivot brackets first, rounding their ends and drilling the centered 5/16"-diameter bolt holes. Mild steel is easier to drill and aluminum even easier. Personally I like your no miter slot version. And now for an update on this project. Looking at the different lengths of material I commonly cut on the band saw, I decided that a 12 30 table would suit my needs well, offering ample support without being unnecessarily long which would make it heavier, more prone to sagging and more difficult to store when not in use. Manage Consent. Adjust and reclamp the leg parts as needed until the outfeed table is flush with the saw table. This workstation has it all a space-saving, fold-down workbench, easy-access tool rack, and a wall-mounted cabinet. So, I did what any sensible person would do. Then, use the brackets to set the width of the dadoes in the filler piece so you'll arrive at a nice, snug fit. Small Adjustments, Big Benefits Wong bored a slightly oversized hole in the rail so it could be adjusted up or down. Chris is a sculptural woodworker and instructor. Mostly I do cabinets but would like to make some chests as well. If you are a carver or want Intarsia, fretwork, intricate design cutting and more! For these items, please call the store where you purchased them or our customer service department at 1-800-376-7856 so we can assist you. I have noticed that Im just not as strong as I used to be. Therefore if placed in line with a mitre slot it would interfere with the sled runner. Attach it to your saw cabinet with three short carriage bolts, washers and locknuts. Obviously, a large amount of time to be spent in ripping plywood.
Relief, 3D, chip-carving, whittling; carving knives, chisels, pocket-knives, power tools. If you're tired of struggling with sheets of plywood, order yours today. I shouldhave put that in my update when I had teh chance. The International System of Units (SI), more commonly referred to as the metric system, is the alternative set of units that we have available for some of our plans. However, if you want even more granular detail to make your job easier, you should consider our premium plans. So, having considered the problems faced with cutting these sheets, I made a list of must-haves. Plane it down so the top face will be about 1/16" below the saw table when its attached to the fence rail. Any thoughts, or do you just make the fit very tight? Using an Infeed and Outfeed Table on a Table Saw will make fast, accurate work out what was a once dreaded process. At best you end up with a less than perfect cut, which has burn marks on it. The store will not work correctly in the case when cookies are disabled. @ Jerry - "Do you not have the fence with the extention for your miter gauge?". Mark and cut the front edging (piece 8) to length, then glue and nail it in place. I got on the internet and started searching for a better way to rip sheet goods. The United States Customary System of Units (USCS or USC), more commonly referred to as the English or Imperial system, is the standard set of units for our plans. Can I sell you on the idea of a crosscut sled? After about the fourth sheet, I had knocked over my trusty roller stand as many times. It helps protect the edges of the MDF and laminate. Slip a couple of 1/2"-thick spacers in between. Drive a brad through each corner to keep the pieces from shifting during clamping. This luxury residential space included a fair number of cabinets, including two kitchens, a library, and a few built-ins, as well as some high-end furniture. I have one also but I am getting a lot of use out of the Incra Miter Gauge. I've tried using a worktable back there, but it's just one more fixture to get in the way in a small shop, and, I've never found a roller stand that provides the amount of stability I want. Another method is to place the sheet on the table, then lift the end of the sheet, and slide the roller stand under it. I managed to get two more sheets cut before the pain forced me to stop once again. This planter bench will offer a seat to anyone who needs it and add colour to the area with some flowers. In fact, we use our Infeed unit in combination with a rip sled, to joint the edges of rough lumber. The finish, whether paint, wax, stain, or something else, can make or break a project. This is exactly how many wood shop related back injuries occur. And they fold for easy storage, when not in use. Price and other details may vary based on product size and color. A small-shop delight, this project is a sweet upgrade to your shops centerpiece. You could make yours even wider if you like, but remember that the leg should be relatively centered underneath for stability. Be sure to double-check the plan before building. Help us spread the word about Woodsmith Plans & earn money at the same time. I think I need one of these! Your email address will not be published. Chat with your Forum Friends about their projects, their life, thei https://www.izzyswan.com/Store/In-Feed-Table-for-Saw-Stop-Table-Saw-p223491307, https://www.izzyswan.com/Store/In-Feed-Table-for-Standard-Table-Saws-p237211510. Check out our Editors recommendations for project supplies and hardware. I think I need one of these! These come with additional shop diagrams that we drew when creating the prototypes. HOT DEALS 2.0: Coupons, Sales, Black Friday, eBay, Amazon, BORG, Zoro, Woodcraft, etc. It all but eliminated the danger of a kick back, and since I was no longer standing behind the sheet, I wouldnt have been hit by the sheet if there was a kickback. Checked his website and they are no longer available for sale. I made one small and one long. I could actually roll the sheet onto the infeed table. Ordinary barrel-bolt hardware locks it quickly in the up position, so I never have to futz with the setting. Stock Support and a Repetitive Cut Flip Stop, Miter Saw Fence w/Laser Marking Scale. Cut the leg extension (piece 14) to width and length, and bevel-rip both of its edges at 35 so it fits well between the guide strips. tips? When not in use it can easily be removed and stored out of the way. I needed something that was easy to put on and take off my saw. Table Saw with Folding Stand, Shop Fox W1720 Aluma-Classic Fence with Long Rails, Grizzly Industrial T28048 - Portable Series Router Table, Rousseau 2790-EXT Extension Table for Models 2790 and 2775 Table Saw Stands, DEWALT Planer Stand,with Integrated Mobile Base (DW7350), Bora Centipede 4x8 15-Strut Work Stand and Portable Table | XL Sawhorse Support with Folding, Collapsible Steel Legs, CK15S, ToughBuilt - 10' Gravity Miter Saw Stand with Universal Tool Mounts - Easy Storage Folding Saw Stand with Rubber Tires - (TB-S600), Grizzly Industrial G0869-10" 2 HP Benchtop Table Saw, Rousseau model 2780-EXT Extension Table For Models 2780, 2700-XL & 2745 Table Saw Stands (REPLACES: model 2710-XL), SUPERMAX TOOLS 16-32 Folding Infeed/Outfeed T, SuperMax Infeed Outfeed Tables, ToughBuilt - Folding Sawhorse/Jobsite Table - Sturdy, Durable, Lightweight, Heavy-Duty, 100% High Grade Steel, 41.5-Inch Easy Carry Handle - (TB-C550), GRR-RIPPER 3D Pushblock for Table Saws, Router Tables, Band Saws, and Jointers by MICROJIG, Grizzly Industrial G0696X - 12" 5 HP 220V Extreme Series Table Saw, VEVOR Precision Miter Gauge, 24" Aluminum Table Saw Miter Gauge w/ 60 Degree Angled Ends for Max. The idea of laying the sheets on a bench, or the floor, on top of a piece of styrofoam, and cutting them with my Festool Saw and track system would have worked okay but was certainly not convenient, or even practical. Attach the leg to the table pivots with bolts, washers and nylon lock nuts (pieces 16). Not only will these units make ripping sheet goods easy, but in our shop, we use it to rip heavy boards too, as shown in the picture on the right. Installing the mounting plate onto the table saw stand and prepping it to receive the outfeed table. I have had mine for a couple of years. Adjust the leg to the approximate required height, then position the dado of the extension table over the rail. I have been wanting to do the same for a long time so I'll be interested to see your results. Thanks for posting. They are used in High School Shops, College Wood Shops, Municipalities, Tech Schools, and many businesses that have a need to cut sheet goods. Patented Infeed and Outfeed units designed by the creator of Pro Woodworking Tips! Now, glue, clamp and nail the side edging to the core with 1-12" brads. We have also sold a number of these units to Ikea Stores, for use in their shops. For a shop-made table, a plastic laminate-coated surface is a great choice and well within the capabilities of most woodworking shops. Rout a 5/16 wide groove for a 1/4 bolt along the center of each outside post, stopping 2 from each end. I decided if I am going to get this done, I needed to come up with some way to make it easier. You can download the additional shop drawings that you purchased using the link in this box. After struggling with ripping long lengths of material on my band saw, I decided to address the issue by building an extension table and mounting rail system to allow the table length to be increased when necessary but stored out of the way when not needed. https://www.izzyswan.com/Store/In-Feed-Table-for-Saw-Stop-Table-Saw-p223491307. The very people who would be most helpful in the shop were also the most important at the site. For a better experience, please enable JavaScript in your browser before proceeding. Great idea, thanks. I built an adjustable leg to support the other end of the table. Many new cabinet saws have a side extension table, and theyre a big help for supporting wide sheet materials or long workpieces when crosscutting. Doesnt even touch the other applications for large, and unwieldy parts. When the table is folded down, this bolt keeps the leg retracted. As I mentioned before, you could attach the mounting rail, then machine the dado on the underside of the support table to suit. Straight Bit Set - 1/2" Shank, Rockler Piloted Flush Trim Router Bits - 1/2" Shank, Jet ProShop II Table Saw with Cast Wings, 115V, 30'' Rip, Video: Eight Tips for Making Sliding Doors, High-quality brands and products you can trust, Expert advice and free post-purchase support, Exclusive, innovative products that help you Create with Confidence, Detailed instructions, technical specs and guides to make the most of your purchases. Questions and answers about CNC machines, tooling, best practices, and projects. To attach the rail, I first put a 2-1/2 long 1/4-20 bolt through the rail followed by a spacer about 5/8-3/4 long. One such project was the renovation of a 6,500 square foot condominium. Ive been wondering if the toggle clamp would be solid enough any thoughts on that? Ease all the sharp edges of the trim with a 1/8" roundover bit, a file or a block plane. Wood, your hand tools, you and a little know-how. Bolt the plate to the metal fence rail with five lag screws and washers(pieces 21) spaced evenly along its length. The shape doesnt matter as long as there is one straight edge to go against the machine table. Next, cut the spacer and build-up strip (pieces 17 and 18) to shape, and fasten them together with one pair of their ends flush. Time to get this project mounted up! Still, they do have some limitations. What made it worse was the fact I was working alone, since my employees were busy at the job site. Your order will come with a return form with convenient instructions, or you may send your returns directly to Returns Department, Rockler Woodworking and Hardware, 4365 Willow Drive, Medina, MN 55340. 2022 Verticalscope Inc. All Rights Reserved. frustrations?
Poke a 5/16" brad-point bit into each table pivot hole, and tap it with a hammer to mark the ends of the mounting plate for pivot screw holes. If the extension table will go over a work surface or other machine top, you could use a set of shims instead. Since I wasnt holding any of the weight, I simply had to steer the sheet across the roller balls. After viewing product detail pages, look here to find an easy way to navigate back to pages you are interested in. Whether you size the rail to the support table or vice versa, the end result should be the same. To secure the table to the rail, a simple rail clamp is employed. First, it had to attach to the saw, so it couldnt be knocked over, or be knocked out of alignment to the fence. Having a large enough band saw tabletop that can fully support your workpiece can improve accuracy, reduce user strain and improve the quality of your work. This pint-size bench is big on options to give you a solid grip on all kinds of workpieces and raise them to a more comfortable level. :dance3: You might be wondering "How did he keep the project still while he routed the edge with the flush trim bit?" It provides a feature-packed home for your saw. Shop products from small business brands sold in Amazons store. Use a straight edge to see if the extension table is planar to the machines table and raise or lower the leg as required. With appropriately mounted rails, an extension table can be used on the infeed or outfeed side of a machine, as well as on the left or right. Listen for the sound of the bit cutting into the metal. Built this clip-on infeed support, and found it to be very handy when using sleds. Also, make sure to locate your holes far enough from any reinforcing webbing underneath to allow a washer to sit flat. We are proud of the quality of our products, and we stand behind them 100%. All the weight is hanging off the table at times. (I know, I know this is a lot of holes to put in your trusty saw, but it's worth it!) Looking for help with Are you unsure of which tools, or hardware, you need, or which brands to buy? Here is a video showing how it works and how to make one: Video. For effective clamping, its important to ensure the batten is kept parallel to the bottom of the mounting rail. 2, Building Base Cabinets For Kitchens pg.
Attach the leg to the extension table with a strap hinge. If you arent able to keep the sheet tight to the fence, you end up with a crooked cut. Screw the spacer to the table and the barrel bolt to the build-up strip. (I used a steel bearing spacer from a pair of old roller blades, but any small tubing resistant to compression would work. Thanks. Drive countersunk screws through the back and into the strips to reinforce these important load-bearing joints. Plywood, MDF or solid wood is suitable for light-duty use, although none of these are as flat, stable, wear-resistant or slick. I opted to do it the other way around, but theres no true right or wrong. Make sure to adjust your tables front-to-back size, if needed, so it won't interfere with the dust port when you fold it down. I started thinking, there must be a solution to this. Kickbacks occur when a piece binds the blade, causing the piece to be thrown back at the operator with amazing force. Youre seeing this ad based on the products relevance to your search query. I suggest widening the leg to broaden its stance if you make a substantially wider outfeed table. Wrap up by cutting the table pivot brackets to final length, gluing and screwing them in place to beef up the pivot points. After five years of hard use, the prototype for the fold-down table you see here has become an essential feature on my cabinet saw. The deeper you mill your dado in the underside of the support table, the weaker the support table will be. You could even mount multiple extension tables in a series for extra length. It provides a 30"-deep platform behind the machine plenty of room to keep long rip cuts from tipping off into the netherworld and its triangulated design is sturdy as can be. Laminate a thick blank of lumber together to form the mounting plate (piece 20) that attaches to the saws fence rail. Since I wanted a compact leg that was also tall enough for use at my band saw, I built a three-tier leg, but you could make a simpler two-tier leg if you dont need that range of adjustability just omit one outside part and one set of hardware. And it extends to create a large work area to tackle almost any size workpiece. Thats because more likely than not the roller stand gets knocked over in the process. Holding up a 40-pound sheet, and trying to bend over to lay the sheet onto the saw table is a terrible strain on the back. The small size of the saw table makes it nearly impossible to cut large workpieces like plywood and MDF. With our unique mounting system, they mount and dismount to the saw in seconds, making them convenient to use, even if you're only making one cut. At the bottom of the leg, install a cross dowel and thread in a 1/4-20 adjustable foot for making fine adjustments to the height. Benchtop table saws are designed for rough-and-tumble work at a jobsite. Having difficulties reading project plans? Niagara on the Lake ON L0S 1J0, 1-800-204-1773 It's true! When I designed my original outfeed table, I wanted the leg to extend and brace against the saw cabinet but also retract so it could tuck behind the table when folded down. JavaScript seems to be disabled in your browser.


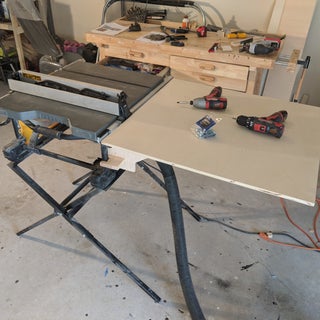
Poke a 5/16" brad-point bit into each table pivot hole, and tap it with a hammer to mark the ends of the mounting plate for pivot screw holes. If the extension table will go over a work surface or other machine top, you could use a set of shims instead. Since I wasnt holding any of the weight, I simply had to steer the sheet across the roller balls. After viewing product detail pages, look here to find an easy way to navigate back to pages you are interested in. Whether you size the rail to the support table or vice versa, the end result should be the same. To secure the table to the rail, a simple rail clamp is employed. First, it had to attach to the saw, so it couldnt be knocked over, or be knocked out of alignment to the fence. Having a large enough band saw tabletop that can fully support your workpiece can improve accuracy, reduce user strain and improve the quality of your work. This pint-size bench is big on options to give you a solid grip on all kinds of workpieces and raise them to a more comfortable level. :dance3: You might be wondering "How did he keep the project still while he routed the edge with the flush trim bit?" It provides a feature-packed home for your saw. Shop products from small business brands sold in Amazons store. Use a straight edge to see if the extension table is planar to the machines table and raise or lower the leg as required. With appropriately mounted rails, an extension table can be used on the infeed or outfeed side of a machine, as well as on the left or right. Listen for the sound of the bit cutting into the metal. Built this clip-on infeed support, and found it to be very handy when using sleds. Also, make sure to locate your holes far enough from any reinforcing webbing underneath to allow a washer to sit flat. We are proud of the quality of our products, and we stand behind them 100%. All the weight is hanging off the table at times. (I know, I know this is a lot of holes to put in your trusty saw, but it's worth it!) Looking for help with Are you unsure of which tools, or hardware, you need, or which brands to buy? Here is a video showing how it works and how to make one: Video. For effective clamping, its important to ensure the batten is kept parallel to the bottom of the mounting rail. 2, Building Base Cabinets For Kitchens pg.
Attach the leg to the extension table with a strap hinge. If you arent able to keep the sheet tight to the fence, you end up with a crooked cut. Screw the spacer to the table and the barrel bolt to the build-up strip. (I used a steel bearing spacer from a pair of old roller blades, but any small tubing resistant to compression would work. Thanks. Drive countersunk screws through the back and into the strips to reinforce these important load-bearing joints. Plywood, MDF or solid wood is suitable for light-duty use, although none of these are as flat, stable, wear-resistant or slick. I opted to do it the other way around, but theres no true right or wrong. Make sure to adjust your tables front-to-back size, if needed, so it won't interfere with the dust port when you fold it down. I started thinking, there must be a solution to this. Kickbacks occur when a piece binds the blade, causing the piece to be thrown back at the operator with amazing force. Youre seeing this ad based on the products relevance to your search query. I suggest widening the leg to broaden its stance if you make a substantially wider outfeed table. Wrap up by cutting the table pivot brackets to final length, gluing and screwing them in place to beef up the pivot points. After five years of hard use, the prototype for the fold-down table you see here has become an essential feature on my cabinet saw. The deeper you mill your dado in the underside of the support table, the weaker the support table will be. You could even mount multiple extension tables in a series for extra length. It provides a 30"-deep platform behind the machine plenty of room to keep long rip cuts from tipping off into the netherworld and its triangulated design is sturdy as can be. Laminate a thick blank of lumber together to form the mounting plate (piece 20) that attaches to the saws fence rail. Since I wanted a compact leg that was also tall enough for use at my band saw, I built a three-tier leg, but you could make a simpler two-tier leg if you dont need that range of adjustability just omit one outside part and one set of hardware. And it extends to create a large work area to tackle almost any size workpiece. Thats because more likely than not the roller stand gets knocked over in the process. Holding up a 40-pound sheet, and trying to bend over to lay the sheet onto the saw table is a terrible strain on the back. The small size of the saw table makes it nearly impossible to cut large workpieces like plywood and MDF. With our unique mounting system, they mount and dismount to the saw in seconds, making them convenient to use, even if you're only making one cut. At the bottom of the leg, install a cross dowel and thread in a 1/4-20 adjustable foot for making fine adjustments to the height. Benchtop table saws are designed for rough-and-tumble work at a jobsite. Having difficulties reading project plans? Niagara on the Lake ON L0S 1J0, 1-800-204-1773 It's true! When I designed my original outfeed table, I wanted the leg to extend and brace against the saw cabinet but also retract so it could tuck behind the table when folded down. JavaScript seems to be disabled in your browser.