The Fuse 1 delivers industrial power in a small footprint with effective powder containment and easy setup. The nearest thing to nylon it prints is Tough Resin. To aid with the powder removal step, users will find it handy to make use of the vacuum cleaner included in the box. To support the new printer and provide users with an end-to-end SLS workflow, the company also launched the Fuse Sift, a post-processing system for the Fuse 1, and Nylon 12 Powder. It's also extremely strong. This has proven to be a highly useful workflow overview tool. Boasting affordability compared to industrial SLS 3D printers, low maintenance and maximum uptime, the Fuse 1 ticks all the right boxes for designers and engineers. Used in conjunction with the Fuse 1, the Fuse Sift is an automated post-processing system designed to depowder polymer 3D printed parts. Additionally, the build chamber is modular in that it can be removed in its entirety. It was designed, printed, and painted by Solid Print3Ds Benjamin Keyser. Elongation at break is rated at 11 percent on the X/Y axis and six percent on the Z axis. Then the part is moved over to the middle of the workspace where the sieve can be found this is where the powder removal takes place. The parameters that Formlabs has chosen work exceptionally well and result in high-quality prints every time, although it does mean that the system is only compatible with the companys own Nylon powders. Coupled with the Fuse 1, the post-processing station makes powder removal and recycling as streamlined as can be, resulting in a well-designed, entirely end-to-end SLS 3D printing workflow. Not only will the Fuse 1 help Formlabs expand its own footprint in the industrial 3D printing space, the company feels it will substantially expand the market size for industrial 3D printing as a whole by offering truly production-ready 3D printing to an entirely new set of customers. The Formlabs Form 2, the best desktop SLA 3D printer on the market today, doesn't support nylon for this reason. In this case, both objects feature internal cavities and a plethora of holes that allow us to judge how the Fuse 1 prints complex geometries without any support structures. Markforged X7 Digital Forge Industrial Fleet Solution, Markforged X7 Digital Forge Industrial Quality Solution. The Ytterbium Fiber 10W laser provides a laser spot size (FWHM) of 200 m (0.0079") and is capable of producing a layer thickness of 110 m (0.004"). Nylon, perhaps, is the most versatile of all materials. With such an awesome description, you'd think that the Fuse 1 could replace any old 3D printer you have lying around. Fuse 1 gives us the design freedom needed to truly customize our prosthetics and the high productivity and throughput necessary to quickly get this solution to our patients.. The streamlined printing workflow coupled with the reliable and refined processing parameters of the PreForm slicer make the Fuse 1 an ideal system for short-run functional applications. For the best experience on our site, be sure to turn on Javascript in your browser. JavaScript seems to be disabled in your browser. Selective laser sintering uses a laser to precisely fuse nylon powder into lightweight, robust parts. SLA, invented in the 1980s, was the first 3D printing process created and uses a laser to cure liquid resin into hardened plastic in a process called photopolymerization.
The sieve comprises a wide grid of small holes that allow unused powder to pass through, while catching larger lumps of powder that have been heated and fused together. Buy the Fuse 1 and Fuse Sift here. Nylon 11 has a 48MPa ultimate tensile strength rating, with 35 per cent elongation at break. The use of the roller allows for improved powder packing and a more uniform powder distribution, which is crucial for achieving high part qualities. We partner with a wide range of manufacturers with over 30 different printers between them, capable of printing in a variety materials from PLA to metal. One of the main selling points of PreForm is that it only has one set of predefined process parameters that cant be modified. So, in March of 2014, Formlabs asked itself if there was anything the company could do to make SLS, a process in which a high-powered laser fuses small particles of polymer powder into the final part, more accessible. The Fuse 1 is compatible with the Fuse Sift for a streamlined process. The Formlabs Fuse 1 is aSelective Laser Sintering (SLS) 3D printer. Based in Somerville, Massachusetts, Formlabs is undoubtedly one of the biggest names in professional-grade SLA 3D printing. Available today, starting at $18,499 for the printer or $31,845 for the complete setup including the Fuse Sift, Formlabs claims the Fuse 1 enables users to take control of their entire product development processfrom iterating on the first concept design to manufacturing ready-to-use products in production-ready nylon. With the Fuse 1, you can 3D print high-performance machine parts, tools, living hinges, jigs, jaws, and fixtures. We visited the offices of UK-based 3D printer supplier Solid Print3D to review both of these devices.Prefer to watch a video of this review? Selective Laser Sintering is one such option, and Formlabs thinks so too. You can make do by making your print in pieces, and then assembling, however, sometimes you'll just need a larger build area. In the end, the Fuse 1 and Sift are a formidable duo and any criticisms are dwarfed by the sheer value offered by these systems. The tank is fitted with a rubber seal to stop any used powder from accidentally mixing in with the fresh powder prematurely. You can print housings, casings, shells, and electronic components. At a minimum, you should always have a mask when using Sift or a media blaster. Similarly, the printer did an excellent job with the planetary gear system. Our measurement devices are accurate to 0.015mm.
Users can reduce downtime thanks to the modular build chamber, allowing them to transfer build chambers and powder cartridges between the Fuse 1 and Fuse Sift for a nonstop, cyclical workflow, according to the company.
Under development for nearly seven years, the Fuse 1 marks a notable change for Formlabs as they expand into a new additive manufacturing process. Then theres the Fuse Sift. That makes it super-tough. The Fuse 1 by Formlabs is a high performance, compact, affordable Selective Laser Sintering (SLS) platform. Connectivity options include USB, Wi-Fi, and ethernet, so feel free to take your pick.
Nylon isabrasion resistant, heat resistant, and has a low friction coefficient. Having debuted its original Form 1 system almost a decade ago, the firm has since packed out an extensive portfolio of resin-based 3D printers such as the Form 3+, Form 3B+, Form 3L, and Form 3BL. Nylon 12 offers flexural strength of 66 MPa and a flexural modulus of 1,600 MPa, according to the company. For more about how we use cookies, please see our, Formlabs Fuse 1 Workflow Essentials Package. Formlabs says the Fuse 1s cooldown times allow users to utilize a second removable build chamber and start printing 12 hours after the previous print has finished. The company discovered that if they treated the printed parts edges with very low energy input, they could keep the bulk of the part printed at full energy density and maintain its mechanical properties all while using low energy density on the edges to prevent birchbark from forming.
Users will also find the stacking feature to be particularly useful especially on an SLS machine as it helps makes full use of the build volume. The company notes that the cheapest commercial SLS 3D printer currently on the market costs around $200,000 and prices can reach as high as $800,000 to $1,000,000. SLS allows designers to create complex interior components using unique geometries, and it allows engineers to reproduce parts with precise replication. Copyright 2022 Printlitic. The parts proved ready to use straight out of the build chamber, with minimal post-processing required and excellent surface finishes all around. Additive manufacturing is thriving and continues to gain momentum with successes across diverse applications. The 3D printed puzzle cube was undoubtedly one of the most spectacular objects we were able to print with the Fuse 1. The IR sensor is what measures the temperature of the powder while the cassette is the element through which the infrared waves and laser beam pass through to reach the powder bed. The V6 engine block and exhaust manifold are typically the kinds of parts a carmaker would prototype in the design phase of a new model. It uses Selective Laser Sintering 3d printer technology. So, if you want to 3D print with nylon, the Fuse 1 is for you. One of the most striking things about the Fuse 1 is its compact frame. Easy. Most of the issues youll run into with the Fuse 1 can be attributed to two of the printers key components: the IR sensor and the optical cassette. You can also stay connected by following us on Twitter, liking us on Facebook, and tuning into the 3D Printing Industry YouTube Channel. As such, the laser moves on the X and Y axes, whereas the bed moves on the Z-axis. All of the models in this section are static, meaning they dont contain any moving parts.
A touchscreen display offers a live stream of the print bed and the camera view is also available from a computer through PreForm so users can monitor their print without leaving their desk.
This enables users to transfer the build chamber to the Sift post-processing station without even seeing the printed part, making powder removal and recycling a breeze. In the best case, 99.6% of the 100mm circles manufactured by this 3D printer will be between 99.93mm and 100.07mm. Each of the gears was defect-free, sported clean surfaces, and meshed well with the rest of the assembly. Ensuring that you choose the right additive manufacturing solution for your application is our priority and we know that one size rarely fits all. This is because of the technology, not the material; a mechanical print head, as all FFF 3D printers have, limits the geometries that are possible during the print process. It makes quick work of the powder that will inevitably scatter all over the workspace, so be sure to give the Sift (and Fuse 1) a thorough cleaning after every build. There's no need for support structure on any model design, and you can print consolidated models in one sitting. The Fuse 1's layer height of 0.11 mm provides smooth surface finishes and detail, while its build area of 165 mm x 165 mm x 300 mm gives you the creative space to create large objects without sacrificing detail. Whether that's to create jigs, jaws and fixtures, or casings for consumer electronics, there's always something. But the Fuse 1 is different because it prints nylon. On the software performance side, theres not much to complain about at all. The store will not work correctly in the case when cookies are disabled. We found the user interface to be highly refined and easy to navigate with minimal latency nothing to criticize here. This printer should be your go-to printer if you are a small business owner whose customers are getting rid of the quality that FDM and SLA printers provide. Nylon 12 is the first powder material for the Fuse 1, but Formlabs noted Nylon 11 will be coming soon, while a flexible TPU and other materials are in development. Below youll find the bell curves for the best and worst circles in the test circle three for the X-axis and circle two for the X-axis. Of all the plastic additive manufacturing technologies, it provides users with the highest resolution and accuracy, as well as the smoothest surface finish. SLS is not a new technology, but this is the first time it has been applied to a benchtop 3D printer with industrial-grade results. The suspension system came out beautifully to say the least. #mc_embed_signup{background:#fff; clear:left; font:14px Helvetica,Arial,sans-serif; width:100%;} /* Add your own Mailchimp form style overrides in your site stylesheet or in this style block. As we have no ties to a single manufacturer, we are proud to able to provide expert impartial advice to you and samples from our printers direct to you to assess the print quality and material properties. The average standard deviation also came in at only 0.0395mm, which is a fantastic result. The combination of the Fuse 1 and Fuse Sift makes for a very streamlined end-to-end SLS 3D printing workflow, but there are a few things to keep in mind when using these systems. Accessible radiation is within Class 1 limits, Pressure controlled two stage filtration (replaceable HEPA and carbon mediums).
The Fuse 1 scaling down SLS 3D printing. Despite this office-friendly image, the Fuse 1 is being used for end part production and in larger manufacturing farms. Stereolithography is equally limited, but in a different way; nylon resins are expensive and prone to irregular performance. Formlabs Fuse 1 High Efficiency Package: Recommended set up for efficient SLS workflow, Formlabs Fuse 1 Workflow Essentials Package: Everything required for SLS set up. This year, their latest 3D printer, the Fuse 1, will go on sale. Looking for a career in additive manufacturing? While many industries have been on hold during COVID-19 pandemic, additive manufacturing has been getting red hotproving its value as it helped provide critical personal protective equipment (PPE) and allowed strained supply chains to flex without breaking. Weighing only 114 kg, this 3D printer is light enough to move around your workspace but big enough to print your largest designs.
Featuring patent pending Surface Armor technology, the Fuse 1 creates a semi-sintered shell that prints around the surface of the part, protecting the part during the print process and enabling great surface finish, high reliability, and high refresh rates, according to the company. We kick things off with a circular trajectory test, which is designed to determine the repeatability of the 3D printer in both the X and Y axes. The Formlabs Fuse 1 SLS 3D printer comes with: Please note, this price is for the Fuse 1 printer only. And at the other end of the scale, you can print beautifully-detailed models. As it stands, Fuse 1 users are limited to printing Nylon parts but Formlabs is currently working on expanding its powder offering.
Wed also argue that the option to fiddle around with the slicing parameters or import custom printing profiles could lend itself to previously unseen innovation. Featured image shows the Fuse 1 3D printer. As a result, the Fuse 1 is likely to feel at home in just about any crammed workshop and is portable enough to wheel around without much effort. Due to the fineness of the powder particles, its also recommended to wear adequate PPE at all times when exposed to airborne powder. SLS 3D printing shouldnt be solely for those with big budgets, it needs to be accessible so all companiesfrom startup to big manufacturercan benefit from the design freedom and high productivity SLS 3D printing provides.. Kubi Sertoglu holds a degree in Mechanical Engineering, combining an affinity for writing with a technical background to deliver the latest news and reviews in additive manufacturing. Compared to other SLS 3D printers, the system is highly space-efficient, measuring just 645 x 685 x 1070mm (1655mm tall with the stand). The print preparation program is easy to use with a polished, clutter-free user interface. To complement the 3D printer, Formlabs also launched the Fuse Sift, a post-processing system for use with the Fuse 1. The Fuse 1 is an impressive 3D printer, both in isolation and on the spec sheet. Here, users can fill the Fuse Sift with fresh Nylon powder to be recycled with the used powder previously reclaimed at the sieving station. The Fuse Sift stress-free post-processing. As it stands, the system is able to 3D print two different polymer materials (Nylon 11 and Nylon 12) and Formlabs is working hard to expand the range of compatible powders. Formlabs provides its own slicing software for use with the Fuse 1 PreForm. SLS has practical advantages over FFF or SLA for design and engineering applications. Wed prefer it if Formlabs also allowed the user to access the log files themselves, but this is ultimately a minor gripe with what is an excellent after-sales service. Its also relatively light, weighing in at 114kg without the build chamber or any powder. Additionally, the printer will only fill the build chamber up to the highest point of the nested models, meaning theres no need for excess powder. The nylon powder is proprietary, so it's made by Formlabs to the highest possible specification. Unsurprisingly, the Fuse 1 delivered once again both the electronics casing and the joining component were printed virtually flawlessly.

The sieve comprises a wide grid of small holes that allow unused powder to pass through, while catching larger lumps of powder that have been heated and fused together. Buy the Fuse 1 and Fuse Sift here. Nylon 11 has a 48MPa ultimate tensile strength rating, with 35 per cent elongation at break. The use of the roller allows for improved powder packing and a more uniform powder distribution, which is crucial for achieving high part qualities. We partner with a wide range of manufacturers with over 30 different printers between them, capable of printing in a variety materials from PLA to metal. One of the main selling points of PreForm is that it only has one set of predefined process parameters that cant be modified. So, in March of 2014, Formlabs asked itself if there was anything the company could do to make SLS, a process in which a high-powered laser fuses small particles of polymer powder into the final part, more accessible. The Fuse 1 is compatible with the Fuse Sift for a streamlined process. The Formlabs Fuse 1 is aSelective Laser Sintering (SLS) 3D printer. Based in Somerville, Massachusetts, Formlabs is undoubtedly one of the biggest names in professional-grade SLA 3D printing. Available today, starting at $18,499 for the printer or $31,845 for the complete setup including the Fuse Sift, Formlabs claims the Fuse 1 enables users to take control of their entire product development processfrom iterating on the first concept design to manufacturing ready-to-use products in production-ready nylon. With the Fuse 1, you can 3D print high-performance machine parts, tools, living hinges, jigs, jaws, and fixtures. We visited the offices of UK-based 3D printer supplier Solid Print3D to review both of these devices.Prefer to watch a video of this review? Selective Laser Sintering is one such option, and Formlabs thinks so too. You can make do by making your print in pieces, and then assembling, however, sometimes you'll just need a larger build area. In the end, the Fuse 1 and Sift are a formidable duo and any criticisms are dwarfed by the sheer value offered by these systems. The tank is fitted with a rubber seal to stop any used powder from accidentally mixing in with the fresh powder prematurely. You can print housings, casings, shells, and electronic components. At a minimum, you should always have a mask when using Sift or a media blaster. Similarly, the printer did an excellent job with the planetary gear system. Our measurement devices are accurate to 0.015mm.
Users can reduce downtime thanks to the modular build chamber, allowing them to transfer build chambers and powder cartridges between the Fuse 1 and Fuse Sift for a nonstop, cyclical workflow, according to the company.
Under development for nearly seven years, the Fuse 1 marks a notable change for Formlabs as they expand into a new additive manufacturing process. Then theres the Fuse Sift. That makes it super-tough. The Fuse 1 by Formlabs is a high performance, compact, affordable Selective Laser Sintering (SLS) platform. Connectivity options include USB, Wi-Fi, and ethernet, so feel free to take your pick.
Nylon isabrasion resistant, heat resistant, and has a low friction coefficient. Having debuted its original Form 1 system almost a decade ago, the firm has since packed out an extensive portfolio of resin-based 3D printers such as the Form 3+, Form 3B+, Form 3L, and Form 3BL. Nylon 12 offers flexural strength of 66 MPa and a flexural modulus of 1,600 MPa, according to the company. For more about how we use cookies, please see our, Formlabs Fuse 1 Workflow Essentials Package. Formlabs says the Fuse 1s cooldown times allow users to utilize a second removable build chamber and start printing 12 hours after the previous print has finished. The company discovered that if they treated the printed parts edges with very low energy input, they could keep the bulk of the part printed at full energy density and maintain its mechanical properties all while using low energy density on the edges to prevent birchbark from forming.
Users will also find the stacking feature to be particularly useful especially on an SLS machine as it helps makes full use of the build volume. The company notes that the cheapest commercial SLS 3D printer currently on the market costs around $200,000 and prices can reach as high as $800,000 to $1,000,000. SLS allows designers to create complex interior components using unique geometries, and it allows engineers to reproduce parts with precise replication. Copyright 2022 Printlitic. The parts proved ready to use straight out of the build chamber, with minimal post-processing required and excellent surface finishes all around. Additive manufacturing is thriving and continues to gain momentum with successes across diverse applications. The 3D printed puzzle cube was undoubtedly one of the most spectacular objects we were able to print with the Fuse 1. The IR sensor is what measures the temperature of the powder while the cassette is the element through which the infrared waves and laser beam pass through to reach the powder bed. The V6 engine block and exhaust manifold are typically the kinds of parts a carmaker would prototype in the design phase of a new model. It uses Selective Laser Sintering 3d printer technology. So, if you want to 3D print with nylon, the Fuse 1 is for you. One of the most striking things about the Fuse 1 is its compact frame. Easy. Most of the issues youll run into with the Fuse 1 can be attributed to two of the printers key components: the IR sensor and the optical cassette. You can also stay connected by following us on Twitter, liking us on Facebook, and tuning into the 3D Printing Industry YouTube Channel. As such, the laser moves on the X and Y axes, whereas the bed moves on the Z-axis. All of the models in this section are static, meaning they dont contain any moving parts.
A touchscreen display offers a live stream of the print bed and the camera view is also available from a computer through PreForm so users can monitor their print without leaving their desk.
This enables users to transfer the build chamber to the Sift post-processing station without even seeing the printed part, making powder removal and recycling a breeze. In the best case, 99.6% of the 100mm circles manufactured by this 3D printer will be between 99.93mm and 100.07mm. Each of the gears was defect-free, sported clean surfaces, and meshed well with the rest of the assembly. Ensuring that you choose the right additive manufacturing solution for your application is our priority and we know that one size rarely fits all. This is because of the technology, not the material; a mechanical print head, as all FFF 3D printers have, limits the geometries that are possible during the print process. It makes quick work of the powder that will inevitably scatter all over the workspace, so be sure to give the Sift (and Fuse 1) a thorough cleaning after every build. There's no need for support structure on any model design, and you can print consolidated models in one sitting. The Fuse 1's layer height of 0.11 mm provides smooth surface finishes and detail, while its build area of 165 mm x 165 mm x 300 mm gives you the creative space to create large objects without sacrificing detail. Whether that's to create jigs, jaws and fixtures, or casings for consumer electronics, there's always something. But the Fuse 1 is different because it prints nylon. On the software performance side, theres not much to complain about at all. The store will not work correctly in the case when cookies are disabled. We found the user interface to be highly refined and easy to navigate with minimal latency nothing to criticize here. This printer should be your go-to printer if you are a small business owner whose customers are getting rid of the quality that FDM and SLA printers provide. Nylon 12 is the first powder material for the Fuse 1, but Formlabs noted Nylon 11 will be coming soon, while a flexible TPU and other materials are in development. Below youll find the bell curves for the best and worst circles in the test circle three for the X-axis and circle two for the X-axis. Of all the plastic additive manufacturing technologies, it provides users with the highest resolution and accuracy, as well as the smoothest surface finish. SLS is not a new technology, but this is the first time it has been applied to a benchtop 3D printer with industrial-grade results. The suspension system came out beautifully to say the least. #mc_embed_signup{background:#fff; clear:left; font:14px Helvetica,Arial,sans-serif; width:100%;} /* Add your own Mailchimp form style overrides in your site stylesheet or in this style block. As we have no ties to a single manufacturer, we are proud to able to provide expert impartial advice to you and samples from our printers direct to you to assess the print quality and material properties. The average standard deviation also came in at only 0.0395mm, which is a fantastic result. The combination of the Fuse 1 and Fuse Sift makes for a very streamlined end-to-end SLS 3D printing workflow, but there are a few things to keep in mind when using these systems. Accessible radiation is within Class 1 limits, Pressure controlled two stage filtration (replaceable HEPA and carbon mediums).
The Fuse 1 scaling down SLS 3D printing. Despite this office-friendly image, the Fuse 1 is being used for end part production and in larger manufacturing farms. Stereolithography is equally limited, but in a different way; nylon resins are expensive and prone to irregular performance. Formlabs Fuse 1 High Efficiency Package: Recommended set up for efficient SLS workflow, Formlabs Fuse 1 Workflow Essentials Package: Everything required for SLS set up. This year, their latest 3D printer, the Fuse 1, will go on sale. Looking for a career in additive manufacturing? While many industries have been on hold during COVID-19 pandemic, additive manufacturing has been getting red hotproving its value as it helped provide critical personal protective equipment (PPE) and allowed strained supply chains to flex without breaking. Weighing only 114 kg, this 3D printer is light enough to move around your workspace but big enough to print your largest designs.
Featuring patent pending Surface Armor technology, the Fuse 1 creates a semi-sintered shell that prints around the surface of the part, protecting the part during the print process and enabling great surface finish, high reliability, and high refresh rates, according to the company. We kick things off with a circular trajectory test, which is designed to determine the repeatability of the 3D printer in both the X and Y axes. The Formlabs Fuse 1 SLS 3D printer comes with: Please note, this price is for the Fuse 1 printer only. And at the other end of the scale, you can print beautifully-detailed models. As it stands, Fuse 1 users are limited to printing Nylon parts but Formlabs is currently working on expanding its powder offering.
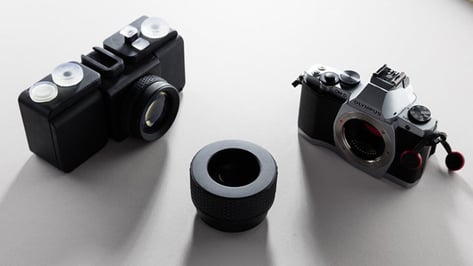

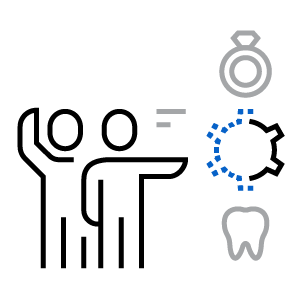