Another factor to consider is that overtime the gas field depletes to lower compressor suction pressure.
Refrigeration compressor types: which is the best solution? 0000011143 00000 n
Note: Comment submission is temporarily unavailable while we make improvements to the site. Careers. This commission helps us pay for the overhead of running this website. For instance, it is not known if small droplets or a liquid film would allow for higher compression efficiency. The efficiency of low rotational speed and low flow rate was improved several points (not shown in fig.2). Other rotating machinery, such as a pump, may also be used to absorb the energy.
0000012032 00000 n
Another main difference is that the precooling is carried out in SWHEs rather than core-in-kettle or plate-fin heat exchangers. 0000001659 00000 n
Electric motors of 65 MW have already been constructed for LNG service. The two-stage compressor operates at lower rotational speed and thus lower stress for a given pressure ratio. 3
eN}G}{F-S>cwL=Bzi)F-'
l6IPjs% `wr Q.E. Intercooling and initial desuperheating is achieved by air cooling. 0000001376 00000 n
1st stage : Wide operating range and high flow rate compressor, 2nd stage : High head and low flow rate compressor. This arrangement has several advantages. Mingxing Bai, Xiaofei Fu, in Renewable and Sustainable Energy Reviews, 2016. The dried compressed CO2 is passed through the carbon beds to remove any mercury that could be present in the flue gas. Since about 1970 a significant and special change occurred with respect to one design feature of the axial compressor and that was the introduction of low aspect ratio blading. The DMR process can be highly efficient in cold climates since the precooling mixed refrigerant can be formulated to avoid temperature and handling limitations associated with propane. 0000076834 00000 n
0000029777 00000 n
The influence of operating conditions (Reynolds number, Mach number, isentropic exponent) on the characteristics of centrifugal compressors and the peculiarities of refrigeration turbo compressors are given by istjakov (1967), Barenboim (1974), Efstafev (1974), Mashimo etal. However, it is not enough for the desired level of offdesign performance, while maintaining the performance at the design point. They concluded that the liquid film contributes to early separation on the airfoil to result in reduced aerodynamic performance. The water vapor centrifugal compressors have been successfully applied in thermal concentrators and water desalination plants. The implementation of a three-port condensing wave rotor in the R718 centrifugal compressor refrigerating cycle is investigated by Kharazi etal. 0000004746 00000 n
It should be noted, however, that this correlation assumes that compressor efficiency is not affected by the liquid in the compressor. The compression train includes water-cooled shell and tube heat exchangers and condensate knock-out drums after each compression stage. HtWr8C?S& ^cOJ9cJ@SE*$4W*%}9}4cxGQTW_V}WJAx$$Gv+s^i{7I]jo? The technology was deployed for the first time at base load scale at the Sakhalin Liquefaction plant in eastern Russia (i.e., two 4.8 MTPA trains using SWHEs and air cooling enhanced by the cold climate), which was commissioned in early 2009. Required fields are marked *. Both of these parameters will impact the production of the gas field. This shows the large-scale application of centrifugal refrigeration machines at the last decade of the century. The compressed flue gas from the scrubber is fed to a dryer unit to reduce moisture content to less than 1ppm. The most popular method of absorbing turboexpander power is by means of a single-stage or two-stage centrifugal compressor, mounted directly on the expander shaft. We'll assume you're ok with this, but you can opt-out if you wish. Fig. A number of power absorption methods are directly applicable to energy recovery expanders. \t~f The total world-wide installations of centrifugal water chillers for air-conditioning applications only were estimated to be about 125,000 (Devotta etal.,1993,1994). 0
endstream
endobj
43 0 obj
<>>>
endobj
44 0 obj
<>/ExtGState<>/Font<>/ProcSet[/PDF/Text/ImageC]/Properties<>/Shading<>/XObject<>>>/Rotate 0/TrimBox[0.0 0.0 612.0 792.0]/Type/Page>>
endobj
45 0 obj
<>
endobj
46 0 obj
[/ICCBased 67 0 R]
endobj
47 0 obj
<>stream
It comprises two centrifugal compressor stages mounted on the same shaft in serial and contained within a single compressor housing. However, there are a lot of problems with the two-stage centrifugal compressor due to limited installation space. As mentioned above, it has been seen in testing that varying droplet size does not cause variation in compressor performance if the liquid flows through a length of suction pipe. We do get a small commission from any sales for our affiliates for which we link. It may be seen that the results of the new model are in good agreement with the simulation results. For the flue gas stream of Table11.3, the flue gas will be compressed to about 25 bara. Within the compression train, some of the trace impurities such as SOx, NOx and Hg will drop out in the condensate collected in the knock-out drums. Similarly, any oxidized mercury present in the flue gas will dissolve in the condensate. <<85BF1FF5AFC57546A42F9B62918F2BAA>]/Prev 834623>>
At the pressure ratio of 3.0, the mass flow range from choke to surge of the two-stage centrifugal compressor was increased by 16% from that of referential singlestage compressor. (2011,2011a,2011b), where the authors show that multistage compression with a flash intercooling strategy between stages results in improvement of coefficient of performance of the water chiller. Technical and environmental advantages of water as a refrigerant and its thermodynamic properties are well known. The efficiency attained by these early, low pressure compressors was about 55%; the reason for this low efficiency is now attributed to blade stall. The machines were used for blast furnace work, operating with delivery pressures between 10 and 100 kPa. 62 0 obj
<>
endobj
In addition, the results obtained from the model are compared with rigorous simulation results from AspenPlus. The mixed refrigerant vapor and liquid are separated and further cooled in the main cryogenic heat exchanger, except for a small slipstream of vapor mixed refrigerant, which is routed to the end flash exchanger (Dam and Ho, 2001). 0000010065 00000 n
HFCs and HFEs are also greenhouse gases, with unknown impact on the environment (Strong,1994). As shown in Figure 1-4, the pinion gear directly engages the low-speed master gear and reduces the speed of the available power to 3,600 or 3,000 rpm, as required. 0000071343 00000 n
Liquid separation is an important topic for wet gas compression research because the outlet of the separator is typically the inlet of the compressor. One of the design challenges is that two compressor impellers are attached to the same shaft. In the latter case large losses would arise as a result of severe stall caused by a large adverse pressure gradient. Thesecompressors have different operating limitations than the reciprocating compressor, the scroll compressor, and the rotary compressor. The idea of water turbo compressor refrigeration systems started at the end of the 1980s and 1990s (arevski,1989,1996; Koren and Ophir,1996; Madsboll and Minds,1996; Paul,2007). 14.35. 0
0000004470 00000 n
The influence of the wet gas conditions on mechanical stability is still unclear. A four-stage centrifugal or reciprocating compressor system is used to increase CO2 pressure to the required injection pressure and it is equipped with suction scrubbers and discharge cooler for each of the four compression stages [21]. 0000073778 00000 n
The turboexpanders frequently used in refrigeration processes develop power, but recovery of this power has often been of secondary importance. If the compressor cannot generate enough pressure head, then the flow rate will be reduced or the delivery pressure will be lowered or both. (2009) and Turunen-Saaresti etal. 0000001054 00000 n
The early difficulties associated with the development of axial-flow compressors stemmed mainly from the fundamentally different nature of the flow process compared with that in axial-flow turbines. When compressors are selected for gas field production operation, they are designed and selected to have an operating map that will cover the various operating conditions that are expected. In this application and many others, the important operating parameters for a compressor are pressure head and flow rate. The process streams, seen in Table 1, are part of a complex refrigeration cycle of a LNG plant. At the core of this issue is the change in the aerodynamic performance of the compressor. As a result of low efficiency, axial compressors were generally abandoned in favour of multi-, shows a graph of the performance of a two-, Adler,1980; Buharin,1983; Japicse,1986, Wuebbles,1994; Kruse,1994; Campbell,1994, show that HFC134a is not a suitable alternative for HCFC22 in existing high-capacity centrifugal units and that there are mixtures that can offer substantially higher capacity, but with a decrease in coefficient of performance (COP). Scheme of two-stage R718 centrifugal compressor heat pump. On these machines, an impeller, casing, and seal are all that needs to be added. The design was based on subsonic flow and the compressor was fitted with variable stagger stator blades to control the position of the low-speed surge line. Between 12th and 14th Streets Since the pressure ratio of each stage compressor decreases, its operating range is extended. So they must be given more consideration when designing a production well [24]. It was not until 1926 that any further development on axial compressors was undertaken, when A. 0000008717 00000 n
0000002462 00000 n
The suction scrubbers remove traces of liquids in the stream and the coolers remove heat generated in compression. 0000028377 00000 n
FIGURE 3-8. A schematic of an R718 two-stage centrifugal heat pump is given in Figure7.3. 0000063132 00000 n
It was reported that the mean aspect ratio ranged from a high of 1.2 in the first stage to less than 1.0 in the last three stages. The pressure ratio between the condensing pressure and evaporating pressure is given in Table2.1 for various condensing and evaporating temperatures. Furthermore, the required pressure ratio (Table2.1, Figure2.1) for a given temperature lift is high. 0000030086 00000 n
The flow within an axial-flow compressor is exceedingly complex, which is one reason why research and development on compressors has proliferated over the years. The development of the theory of measurements and measuring instruments has resulted in a further progress and development of advanced methods for theoretical and experimental investigations of turbo compressors (Dean,1971; Eckardt,1975,1976; Adler,1980; Buharin,1983; Japicse,1986). The minimum approach temperature difference is 5C; cooling water is available at 20 C and returned at 25 C. Additionally, the high value of the water isentropic exponent causes high temperature at the compressor discharge. evaluated several steam turbine erosion models and adapted one for wet gas compressions. If the performance of the compressor significantly changes due to the presence of liquid, then this will cause limitations in the operation of the compressor. A high pressure ratio compressor (550 kPa delivery pressure) was also built by Parsons but is reported by Stoney to have run into difficulties. The design, comprising two axial compressors in series, was abandoned after many trials, the flow having proved to be unstable (presumably due to compressor surge). 14.36) when LMF is <50%. It is estimated that the following specifications are required for each stage of the two-stage compressor. These compounds readily react with water to form sulfuric and nitric acids, which will also be recovered in the condensate. 0000006338 00000 n
Results for different cooling demands, M.M. 0000007000 00000 n
Table1. Generally, the carbon beds are sized such that the change-out of carbon is no more frequent than once every three months. 0000002676 00000 n
0000070624 00000 n
Ransom et al. The main differences arise because in this work the compressor performance is modelled using fan laws, while in AspenPlus, the performance is interpolated between performance curves for different compressor speeds. Fig. The influence of the refrigerant thermodynamic properties on some refrigerating turbo compressor characteristics is presented by arevski (1996). 0000007209 00000 n
A study by Grner et al. Some of these influences are related to thermodynamic type issues (temperature ratio decreases because you have a higher mass of fluid with a higher heat capacity, which requires more energy to have a temperature change) while other influences are related to aerodynamics. Table 2. The performance of axial compressors depends on their usage category. Pacheco et al. More experimental research on the influence of wet gas conditions on the stiffness and damping of internal components is necessary. Numerous CFD techniques (Blazek,2007) and applicative software have been developed in recent years for 3-D unsteady transonic viscid flow and applied for prediction of the flow and performance characteristics of turbo compressors. Ryan Cater, Dirk Bche, in Compression Machinery for Oil and Gas, 2019. The symbols in fig.2 indicate the target points; Figure2. Hall Ph.D., in Fluid Mechanics and Thermodynamics of Turbomachinery (Sixth Edition), 2010. (2007), where the authors show that the water-based vapor compression refrigeration systems will not be economically attractive for a refrigeration unit with nominal capacity of 3520kW (in comparison with the current state-of-the-art technology for large chillers that use R134a) without substantial and successful efforts to develop low-cost, high-capacity compressors. Two beds in a leadlag arrangement are used. A nominal capacity of 3520kW is too large for R718 centrifugal refrigeration units (arevski and arevski,2011b,2012a). By continuing you agree to the use of cookies. (1990), Higashimori etal. Currently, there is no research that identifies a desired flow profile for the gas/liquid mixture at the inlet. The cooling duty for liquefaction of the natural gas is provided by a second mixed refrigerant cycle. It is now widely known that although a fluid can be rapidly accelerated through a passage and sustain a small or moderate loss in total pressure the same is not true for a rapid deceleration. presented a simple correlation of the relationship between wet and dry power requirement based on the mass flow of the liquid and gas. The idea of using a form of reversed turbine as an axial compressor is as old as the reaction turbine itself. Other issues make them not ideal for use in certain applications because of the operating range issues. This means the increase in shaft length and the two impellers running at the same speed make it more difficult to design each stage at its optimum condition. Gabrielii and Vamling (2001) show that HFC134a is not a suitable alternative for HCFC22 in existing high-capacity centrifugal units and that there are mixtures that can offer substantially higher capacity, but with a decrease in coefficient of performance (COP). Another main difference is that the precooling is carried out in SWHEs rather than core-in-kettle or plate-fin heat exchangers. When liquid is introduced into the flow stream, the temperature ratio across the compressor drops, the pressure ratio changes, the power consumption increases, and the flow rate is limited. }~xxhc)DeMc>'8uc{a'$ZXS*+H"S%U=r6KckiccRm[7-=[a!.t#Kexm\SVm3.)jStE]Y/*2rCm#maCl0`C/WS^h}Vd0E-~t-k"j,PvuPU75^T]M/>4jZd3sW7URe HAsE] +X oL^~k 1K=!~2bpfZhu.1H*ph`}nO3nzO
[}T5CK>l+Bs-[$T70VjRabfTTuPYz!}SP.!X15#`>z;RQmA|74mG{ZCw-#}wP/fTPXuSQvF6Q6_7Sp,./pN#^wJMG|HUB~C *68iaTBh^%:D)K4fe2Z
}e KUEln&zj, VFCf;B~PH55L@tOo@6y0iX`^s\qFgTg2jm`GExGEjczSvEAczn$BrXb"^JEDg%0uq-Aw@MFk6. For example, liquid slugging upstream of the compressor can cause the compressor to surge by momentarily starving the compressor of gas flow. Washington, D.C. Email powered by MailChimp (Privacy Policy & Terms of Use), International Media Interoperability Framework. Pressure ratio w for various condensing and evaporating temperatures. 0000002346 00000 n
Deep vacuum operating conditions and the low specific volumetric cooling capacity of R718 (Table2.1, Figure2.1) are peculiarities that cause large and extremely large volumetric flow rates for the temperature range of refrigeration/heat pump air-conditioning applications. The principal objectives of this chapter are: to introduce a calculation procedure and a model for the main parameters, design, flow, and performance characteristics of water centrifugal compressors regarding their peculiarities and operating conditions (high peripheral speed, high Mach number, high pressure ratio, low Reynolds number); to propose recommendations for optimal design of the flow field; to determine the range of suitable application of centrifugal compressors in water refrigeration and heat pump systems; and to provide possibilities for wider application of water centrifugal refrigeration and heat pump systems using the achievements of development of centrifugal compressor technology. Because of the small molecular mass of the water, the R718 centrifugal compressor stage pressure ratio is usually low. Another important part of compressor operation is mechanical stability; whereby operating outside of the normal operating regime can result in significant physical damage to the machine. Some other HFCs, HFEs, and refrigerant mixtures are also used to some extent. 0000020645 00000 n
The refrigerant of this cycle consists of a mixture of nitrogen, methane, ethane, and propane. Figure1. 0000005422 00000 n
proposed a unique back-to-back two-stage compressor arrangement (8). On the basis of the recent developments and technologies considered for oil-free direct-driven variable-speed refrigeration centrifugal compressors (high-speed permanent magnet motor technology, and active magnetic bearing technology), and following the state of the art of material and strength sciences and the achievements in fluid dynamics (CFD), the water centrifugal compressors receive new perspectives and possibilities for future development. The fundamentals and general theory of turbo compressors are given by Eckert and Schnell (1961), Eck (1973), Den (1980), Ris (1981), Seleznev and Galerkin (1982) and many other fundamental publications in the field of turbo compressors. A related later development pursued by the U.S. Air Force was an alternative inlet stage with a rotor mean aspect ratio of 1.32 that produced, at design, a pressure ratio of 1.912 with an isentropic efficiency of 85.4% and an 11% stall margin. 0000070719 00000 n
0000002427 00000 n
The closer coupling between the two cycles by mechanical interlinking of compressors is an operational challenge. Little or no experimental data have been published specifically on erosion in the wet gas conditions described above. The centrifugal compressoruses centrifugal force to sling the vapor refrigerant outward to increase the refrigerant pressure and the temperature and then sends it to either condenser coils or a condenser barrel where the heat is removed from the refrigerant. The process can use either C3 or an MR in precooling. The subject of investigations in this chapter are the water (R718) centrifugal compressors, their main parameters, design and operating characteristics, fluid flow features, and performance characteristics. 0000071248 00000 n
At first, the performance of the two-stage centrifugal compressor was estimated from the single-stage compressor maps measured previously as shown in figure2. The DMR process can be highly efficient in cold climates since the precooling mixed refrigerant can be formulated to avoid temperature and handling limitations associated with propane. However, if the performance of the compressor in wet conditions is influenced by the suction pressure, then the variation must be well understood for operation of the compressor.

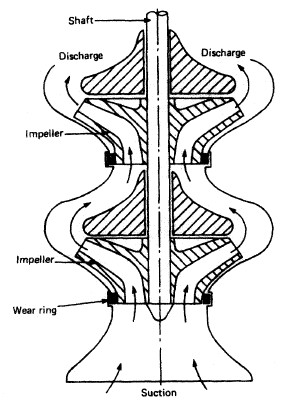